Protective Agriculture Production Series: Fundamentals
ID
SPES-355NP
Fundamentals of the production system
Protected agriculture is still little developed in the Eastern Shore of Virginia (Accomack and Northampton counties) and the Chesapeake area. However, these systems could serve as an important tool for small growers to access niche markets, by providing a setting for new specialty crops and potential season extension. Protective structures, such as greenhouses, tunnels, and shade houses are known worldwide as production systems for high- quality vegetable crops. The most common are ventilation system, structure perpetuity, shape, and height (Table 1).
There are three basic designs used for plant production: greenhouses, tunnels and shade or screen houses, and several variations within each category (Figure 1). A common classification method is based on their ventilation, as structures can be classified as passively or actively ventilated. An active ventilated structure will ensure, within limits, that the temperature and relative humidity inside the structure is constant, regardless of the changes outside. This will require a completely enclosed structure with exhaust or/and ventilation fans, cooling pads for evaporative cooling and in some cases air conditioning to heat up or cool down the air inside, which usually results in a higher investment and maintenance cost. Passive ventilation relies on the structure design and positioning to promote air replacement inside the structure. This is commonly done by building openings across the center-top of the structure roof (ridge vent) (Figure 2) or with side curtains.
Greenhouses can be found in a diversity of shapes and sizes. The most distinctive difference between greenhouses and tunnels is that greenhouses are often permanent structures, while tunnels can be rebuilt every season.
Greenhouses: | Permanent structure with either passive or active ventilation. |
Glasshouse: | (Adapted to snow) fully or semi- enclosed structure with either passive and/or active ventilation, common covering materials are plexiglass, polycarbonate, and/or diffuse glass with or without coating. |
Low-cost greenhouse: | (Recommended for snow free areas) fully or semi- enclosed structure with either passive and/or active ventilation, common covering materials are polyethylene and polycarbonate with or without coating. |
Tunnel: | Non-permanent structure with passive ventilation, solid plastic roof with concave shape, galvanized tubular steel of varying dimeter and thickness and removable doors and sides. |
Shade/Screen houses: | Non-permanent structure with no solid roof or sides. |
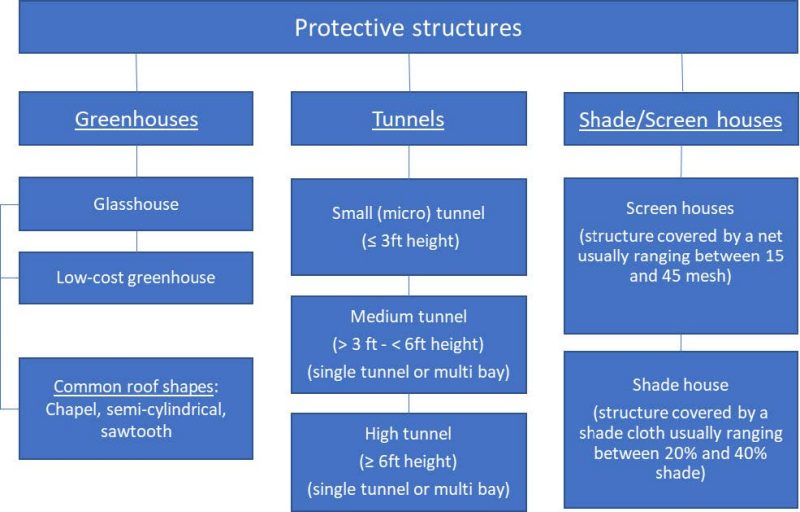
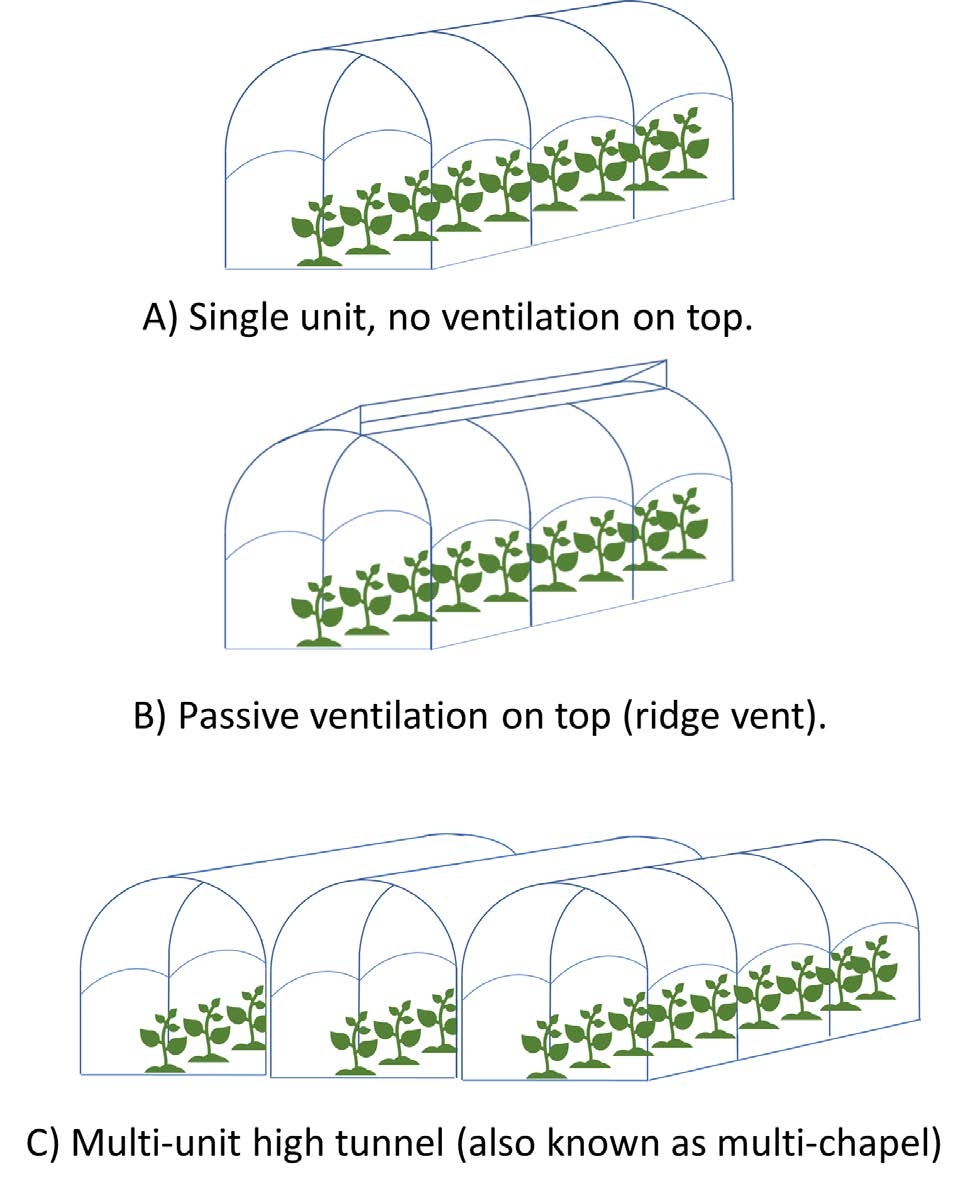
The plastic roof of many protective structures will have a special additive that promotes the homogeneous diffusion of sun light inside the structure. In some regions with minimal radiation restrictions, there will be little to no shading among plants, regardless of their density or trellis system. The radiant light will be both reflected by the plastic roof and diffuse into the structure, which in term will heat up the air inside (Figure 3). If there is no ventilation, the structure will accumulate the heat inside and warm up the crop. A vent on the top of the structure will allow the hot air to scape, as warm air will rise to the top due to its lower density. However, if there is no covering on the sides, there is no need for a top vent as the air will be constantly replaced, and the structure will have a similar air temperature to the open field.
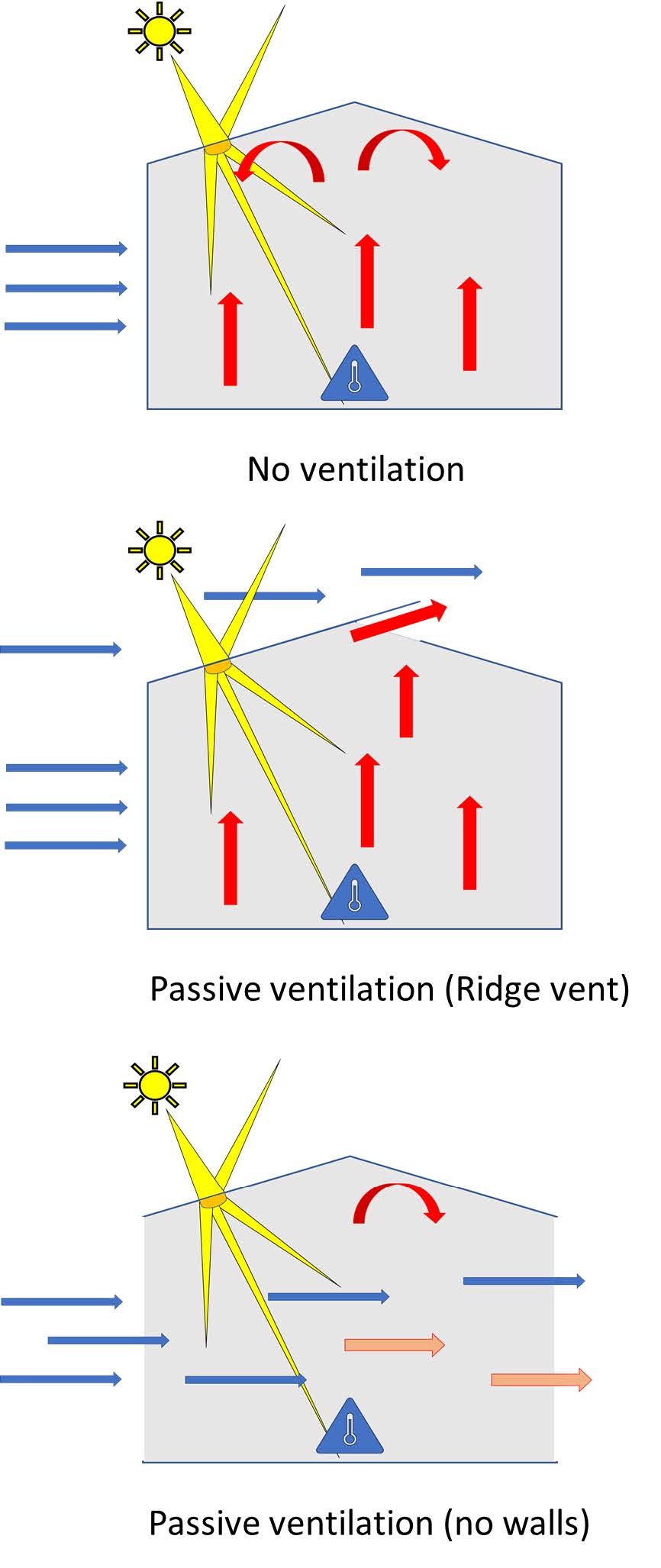
Shade houses and screen houses are types of porous- roof structures. The main difference between them is the color and mesh (number of openings in one linear inch of any screen). Shade houses are usually made of black, red, or blue covers, and they are designed to protect the crop from intense sunlight while decreasing temperature under the structure. Screen houses are usually covered with white nets and will typically protect the crop from high winds and reduce the entry of thrips and aphids. The degree of protection a screen house provides against arthropod pests is correlated to the net mesh. A 60- mesh net will provide a significant level of protection but will also reduce air movement into and out of the structure. A 40-mesh net will allow for a better ventilation but will also provide a negligible protection against pest. A key disadvantage of screen houses is the constant battle between ventilation and level of protection, as low air movement will increase air temperatures. In addition, crop production under screen houses may be limited during the rainy season because of the high incidence of physiological disorders and propagation of disease-causing pathogens.
Regardless of the design, the structure height will play an important role in their internal microclimate. Fully enclosed structures will typically concentrate more heat inside than partially open structures as the plastic walls and roof significantly reduce the air movement, which is constantly accumulating radiant energy from the sun. Hence, the temperature inside the structure increases as the air inside air cannot be replace by the outside air. However, all things equal, a small structure will require less time to increase its inside air temperature than a larger structure, given that the volume of indoor air is lower (Figure 4).
In contrast, a taller structure will require a longer time to heat up, due to the higher volume of air inside. In the same manner, changes in temperature can be drastic in a small structure, as a small opening could rapidly promote air replacement and balance its temperature with the open field. A large structure will take longer to accumulate heat inside, but it will also retain that temperature for a longer time.
In addition, the height of the structure will determine:
- The potential usages of farm equipment under the structure.
- The flexibility of the growing system (gutters for hydroponics, multi-tier baskets, etc.).
- Maximum height for plant trellis (particularly important for suffrutescent stems, e.g., bell pepper).
- The structure heating and cooling speed during summer and winter and potential disease incidence, as improved air movement is often associated with reduced fungal pressure.
The goal of the farmer should be to build a structure that allows the completion of daily farming tasks, while providing an adequate growing environment, and maintaining the system profitability.
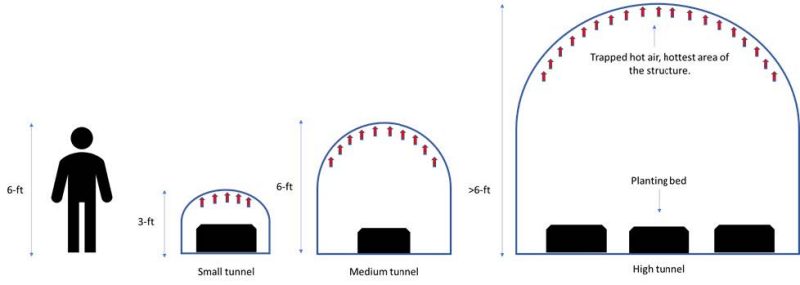
Pest complexes often differ inside a protective environment. Growers should not assume that any protective structure will serve as a complete shield against insects and diseases. The microenvironment inside the structure will promote, in most cases, the correct development of plants, but will also often be conducive for different plant pest.
Types of plastic cover
The national greenhouse manufacturers association classified the covering material into the following types:
Type 1: single thin plastic films, generally ranging from 2 to 8 mils (0.002” ‐ 0.008”), sometimes installed using two layers with air inflation between the layers to provide added insulation. Specific types of films: ethylene vinyl acetate (EVA), polycarbonate (PC), polyester, polyethylene (PE), polyvinyl chloride (PVC), and polyvinyl fluoride.
Type 2: Rigid Plastic panels such as single layer corrugated polycarbonate and fiber glass‐reinforced plastic (FPR); multi‐wall acrylic, impact modified acrylic and poly carbonate
Type 3: Rigid glass materials including annealed, tempered, and laminated.
Different protective structures will have a wide range of prices based on their frame, implements and covering material. These covering materials can greatly differ in their light transmissibility and diffusion, resistance, and weight. Plastic films have lower density and hence lower weight compared to rigid glass. For example, a PE film (1-ft2 wide and 8 mils thick (0.008”; 0.2 mm)) weights about 0.64 ounces (18.3 g), while a rigid glass with the same dimensions and 98 mils thick (0.098”; 2.5 mm) weights close to 21 ounces (596.9 g). If we calculate the weight of an acre of protective material for both examples, the PE film would weight close to 1,742 lb., while the rigid glass would weight nearly 57,172 lb. This difference in weight represents a significant increase in freight and installation cost.
In the same way, a denser material will be more resistant against heavy rain, hail, and snow. Consequently, the primary indicator for covering selection should be the weather pattern of the selected location. Growing plants in an area prone to snow will required a covering material that can withstand the weight (avg. 12 lb/ft3), while a plastic film should suffice for Mediterranean, subtropical, and tropical climates. Areas susceptible to hurricanes and tropical storms should take extra steps to secure their structures.
PE covering is the most common material for protected agriculture around the world. Its low cost, large sheet size, ease of attachment and light transmissibility are properties that have helped to expand its use. Most PE films are manufactured as a coextrusion of three layers with polymers and additives. Each of them contributes to the quality of the film and enhances its performance. The most common additives categories and their applications are listed in Table 2.
Additive* | Application |
---|---|
Hindered amine light stabilizers and/or metal deactivators (HALS) | Reduce plastic degradation due to radiation (deactivate free radicals created by reactions with UV light). Extend plastic life. Susceptible to acidic reaction by pesticides. |
NOR-HAL (HALS with alkoxy (NOR) as an active amine group) | Traditional HALS are basic (nonacidic), and their effectiveness is reduced by acidic environments (can be deactivated by acidic agricultural chemicals (e.g., pesticides); thus less-basic, NOR-group HALS molecules have been developed as the latest generation of radical scavengers. |
UV stabilizers | Extend the life of plastics sensitive to UV light and agrochemicals. Reduce the occurrence and spread of some insect pests. |
Condensate control (anti-drip) | Wetting agent that reduces surface tension allowing condensation to flow rather than form droplets. |
Infra-red films / Infra-red bloquers (termal) | This additive trap the inside radiant heat from escaping. In heated greenhouses, the savings have been measured to total from 10 – 20% depending on whether the sky is cloudy or clear. In areas with strong sunlight, blocking part of the infrared spectrum can lower inside temperature up to 10⁰F. Selective pigments can be added to the outside layer in copolymer film to reflect or absorb the near infrared radiation. |
This list does not represent a complete catalog of all available film additives. Farmers and agricultural professionals should thoroughly understand the benefits and throwbacks of any potential plastic film before purchase.
High tunnels for vegetable and fruit production
High tunnels are a common low-cost option for vegetable growers. The structure is commonly used to protect the crop against cold weather during the winter months and against heavy rain in summer. However, depending on the location, the degree of protection might be more or less pronounced. Production areas with hard winters are a challenging environment for vegetable production, as most vegetables will completely stop growing at 50⁰F or less, showing different damage levels as the temperature keep dropping. In this situation, a tunnel might provide some level of protection for the plant, which depending on the temperature and species (tropical and subtropical), might maintain its normal growing rate, or at least survive the severe outside environment.
Under different circumstances, tunnels can also be used to promote earliness of temperate crops. Many fruit tree species require accumulation of inductive cycles (chilling hours: number of hours at 45⁰F or less – species dependent) to break dormancy. However, after fulfilling their chilling requirement, meristems typically need to accumulate heat units for bud break and flowering. In open field, warmer temperatures may not be achieved until late spring. However, a high tunnel with adequate covering will promote higher air temperatures than the open field earlier and hence, earlier flowering.
During the summer months, high tunnels will provide protection against heavy rain, high speed wind, and small particles that might impact flowers and fruits. It will also protect against many physiological disorders associated with rapid changes in the water and nutrient balance of the growing media (soil or soilless). High tunnels often promote better fruit quality, longer seasons and better control of the irrigation and fertilization practices. Hence, this system can be highly profitable if is adequately manage (Figure 5 and 6).
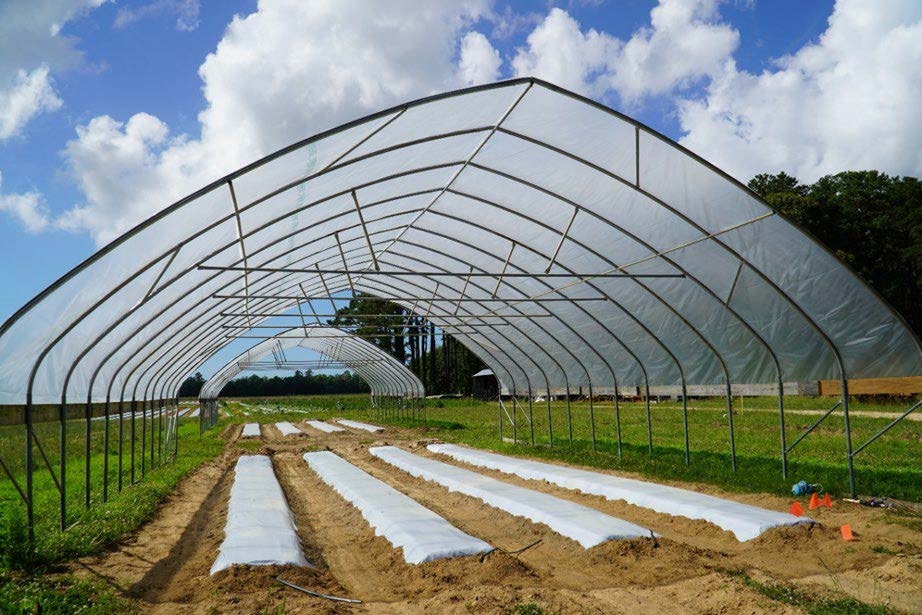
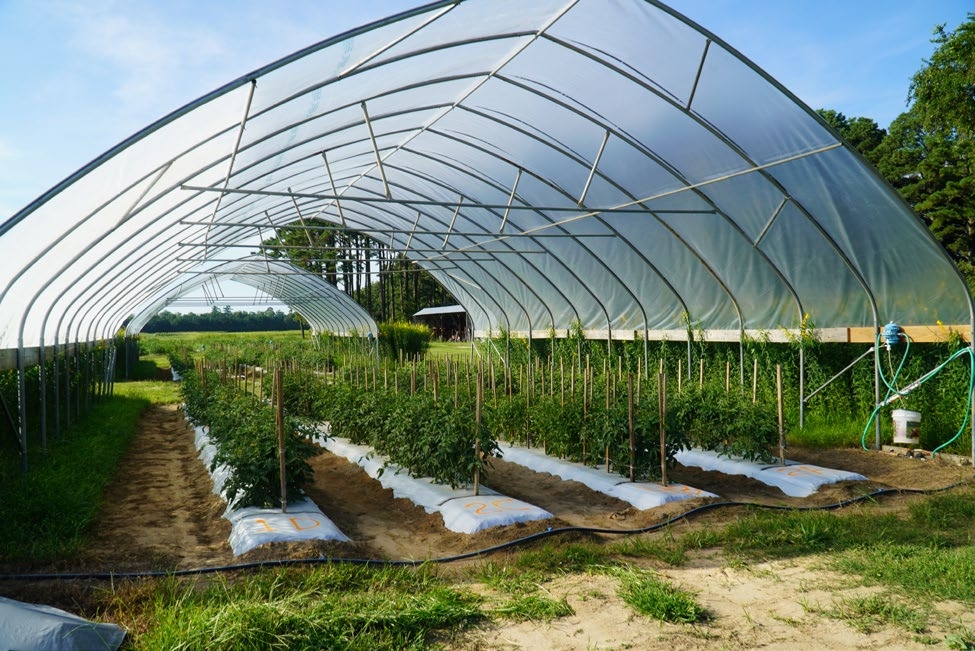
Small farmers at the Eastern Shore of VA could benefit from season extension through November and December and protection from heavy rain events in July and August by implementing high tunnel systems for vegetable production (Figure 7). Nevertheless, research is still needed to identify production practices adapted to the Eastern Shore climate, labor availability, and interactions with price fluctuations of vegetable crops.
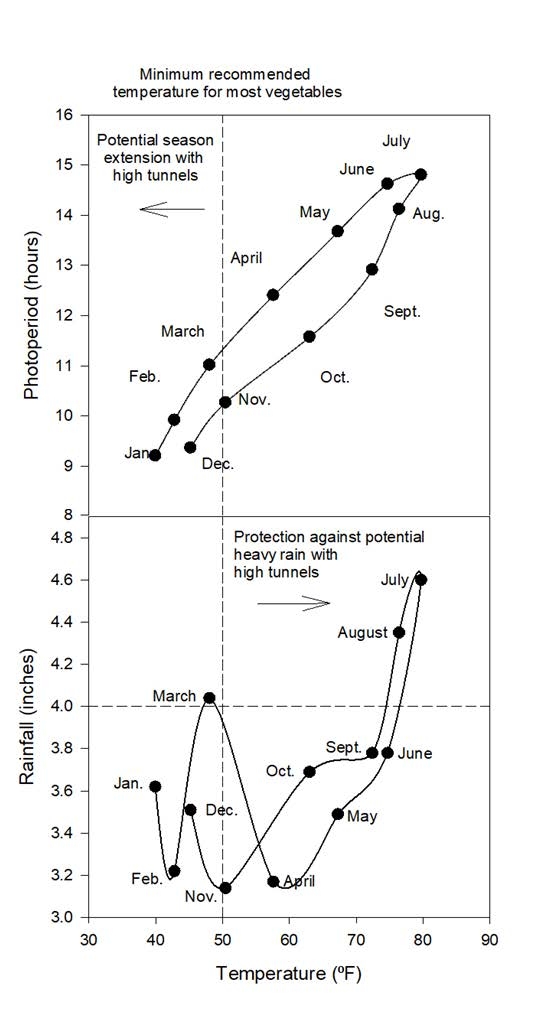
Overall high tunnel can offer growers increased yield and season extension. These structures are lower in cost that traditional greenhouses, thus allowing for possibly better returns on investment depending on the crop produced, markets, and growers expertice.
Virginia Cooperative Extension materials are available for public use, reprint, or citation without further permission, provided the use includes credit to the author and to Virginia Cooperative Extension, Virginia Tech, and Virginia State University.
Virginia Cooperative Extension is a partnership of Virginia Tech, Virginia State University, the U.S. Department of Agriculture, and local governments. Its programs and employment are open to all, regardless of age, color, disability, sex (including pregnancy), gender, gender identity, gender expression, genetic information, ethnicity or national origin, political affiliation, race, religion, sexual orientation, or military status, or any other basis protected by law.
Publication Date
September 16, 2021