Five Strategies for Extending Machinery Life
ID
442-451 (BSE-327P)
Machinery ownership and operation is a major crop and livestock production cost. Several strategies when combined can significantly affect costs, improve machine reliability, and improve profit margins.
How to Get Maximum Machinery Life
This publication discusses five strategies to achieve maximum farm machinery life. These strategies are: machinery maintenance, oil analysis, machinery storage, engine tune-ups, and avoiding modification of tractor engines.
Machinery Maintenance
A study showed that many farmers could reduce machinery repair costs 25 percent by improving routine maintenance procedures. With a yard full of machinery, that savings can be significant. As an example, an $80,000 tractor will typically require about $24,000 in repair costs during 5,000 hours of operation when receiving average maintenance. This cost can be decreased to approximately $18,000 with excellent service management.
Timely preventative maintenance and inspection will not only help reduce major problems and downtime, it will also help identify problems when they can be corrected with relatively minor repairs.
Equipment repaired during the winter can save money on service at mechanics’ shops. An effective machinery service program requires good record keeping. It should not be based on the operator’s feelings or memory as to when a machine needs attention.
The maintenance program must be based on fact as determined by an accurate service record for each piece of equipment as recommended by the operator’s manual and adjusted to individual conditions.
To aid record keeping, mount a service record chart for each vehicle and implement in a prominent area of the farm shop or in a service “record book.” Identify hour maintenance intervals such as 10, 50, 100, 250 and 500 so it is convenient to identify, perform and record the services needed (see Figure 1 at the bottom). Be sure to follow the “Preventative Maintenance Guide” in the operator’s manual for each particular piece of equipment (similar to items at the bottom of Figure 1). Carry a small notepad in each cab to record problems and observations as they arise.
Sample Maintenance Calendar
A large planning calendar is a useful reminder (Fig- ure 1). Use this calendar for noting major repair and service operations to be performed on each piece of machinery in the months ahead. This system is more effective than depending on memory, especially where more than one operator uses the machines. As repairs are needed, make a list on the calendar.
Cover all charts and the calendars with Plexiglas. Record data with a grease pencil; at the end of the year the Plexiglas can be erased and the chart and calendar reused. Maintenance charts may not solve all maintenance problems and they do require work to keep them up-to-date. If extending economic machinery life is the objective, timing of proper maintenance, as recommended by the manufacturer, is the best way.
Oil Analysis
A detailed look at a sample of engine, transmission or hydraulic oil is a valuable preventative maintenance tool. In many cases, it enables identification of a potential problem before a major repair is necessary and downtime during critical operations can be avoided. Oil analysis is a means of monitoring wear and oil contamination. When conducted on a regular basis, it establishes a baseline of normal wear and can indicate when abnormal wear or contamination occurs.
Taking an Oil Sample. It is important to get an oil sample that is representative of all of the oil in the machine. Remember, your analysis will be based only on the sample that you send in for analysis. Always have the oil hot and thoroughly mixed before sampling. Handle hot drained oil with care - it can cause serious burns. The easiest way to obtain a sample may be when the oil is being drained for an oil change. Sampling at this time usually involves letting some of the oil drain and then catching a sample in an appropriate container.
Samples also can be obtained without draining oil by suctioning it out through plastic tubing routed down into the oil reservoir.
In any case, it is important to have an appropriate container and follow sampling directions thoroughly. Remember, many of the tests are for measuring materials on a parts per million basis, so safe, effective sampling is needed.
Cost and Convenience. Cost of oil analysis will vary according to the laboratory and extent of the analysis. Typical charges are $20 to $50 per analysis. The expense can be justified if it alerts the owner to a major problem that can be corrected in the off-season and prevents downtime when the machine is needed. Several companies have developed oil analysis kits that make oil analysis convenient. These kits include the sample bottles, suction pump and tubing, and possibly a pre-addressed, postage-paid mailing container.
Locating a Source. Your local fuel and oil supplier or machinery dealer may be the most convenient and economical source for oil analysis, although not all fuel and oil suppliers or machinery dealers are involved with oil analysis. Independent laboratories are another source and probably can best be located by looking under the classification of “Laboratories.”
Results of the laboratory analysis are typically returned in two to four days after the lab receives the sample. The laboratory may note when the analysis shows an abnormal condition and issue a caution or recommendation accordingly.
Most maintenance experts realize the oil change intervals for both engines and transmissions are decided by the “average need.” No two pieces of equipment have the same preventive maintenance needs. Each machine has different imperfections and is used under different conditions. Operators doing smaller or lighter jobs can cause different conditions on engines and transmission wear than those that occur during more extended use. When using oil analysis to determine maintenance intervals, there is little guesswork. Records show that some equipment can safely run two or three times longer than recommended intervals. The oil analysis may show that you are changing the oil more often than necessary - or not often enough.
By eliminating unneeded oil changes, you reduce the cost for oil and servicing and also reduce the amount of used oil to deal with. This is an important pollution prevention method - reducing the source! Oil sample analysis saves you repair and maintenance dollars, has the potential to reduce used oil, and increases resale value of equipment.
Machinery Storage
The farmer who keeps the most valuable and vulnerable machinery out of the weather can save a lot of money. Equipment stored inside has a significantly higher trade-in value compared to the same equipment stored outside, as shown in Table 1. For example, keeping $600,000 worth of tractors, combines and planters inside, and assuming a 50 percent trade-in value after five years would make this equipment’s value approximately $40,500 more.
Savings 1 | Saving Based on Initial Price TOTAL |
Saving Based on Initial Price Annual |
---|---|---|
Tractors | 16% | 1.6% |
Harvesting Equipment | 20% | 2.0% |
Planters and Drills | 12% | 1.2% |
Tillage Equipment | 5% | 0.5% |
Average Increase | 13.5% | 1.4% |
1Assuming 10 year life.
Inside storage of a small tractor will increase the trade-in value by $400 to $500 per year. Proper storage of a 4-wheel-drive tractor should add $1,000 to $4,000 per year to the resale value. Storage also saves money by reducing repairs and time in the shop.
Machinery stored inside had only 7.6 percent downtime, while unhoused equipment was down 14.3 percent of the time it should have been working. Parts such as belts, tires and hoses deteriorate rapidly when unprotected. Places where water can collect and freeze are problem areas.
To determine the value of stored machinery, add the increase in trade-in value and value of fewer repair costs and subtract the downtime. Now with these values determine the value for storage as a percentage of initial price. Table 2 estimates these savings as a percentage of initial purchase price.
Savings | Greater Value | Fewer Repairs | Less Downtime | TOTAL |
---|---|---|---|---|
Tractor | 1.6% | 1.5% | 1.2% | 4.3% |
Combine | 2.0% | 3.5% | 1.2% | 6.7% |
Planter | 1.2% | 2.5% | 1.2% | 4.9% |
Tillage | 0.5% | 0.5% | 0.6% | 1.6% |
To determine whether a new machinery storage building will pay, you must determine a method to allocate building costs. The building may have alternate uses (i.e., temporary grain storage, repair and service area) and will have a longer life than most implements. Then, compare costs to the expected increase in value of the machines stored on an annual basis.
The estimated annual cost of machinery storage includes depreciation of investment, interest, taxes and insurance. The estimate for machinery storage is $1.25 per ft2 annually.
Machines, including tractors, combines, planters, drills, forage choppers, trucks and pickups, should be kept inside. Tillage implements should be the last to be placed inside. They take up a lot of space and decline in value only slightly faster when left outside. After five years, tillage equipment kept inside is worth only about 5 percent more than if left outside. Usually, the deterioration that occurs to the tires and bearings is less than the cost of providing building space.
Engine Tune-Ups
Diesel and gas engines require periodic tune-ups. As engines operate, they lose power and fuel efficiency. To obtain the optimum performance from an engine, the power produced and the fuel consumed should be checked and compared to the University of Nebraska Tractor Test data. Test reports can be obtained from the Nebraska Tractor Testing Laboratory, Biological Systems Engineering Department, P. O. Box 830832, 134 Splinter Labs UNL, East Campus, University of Nebraska, Lincoln, NE, 68583-0832 (http://tractortestlab.unl.edu/).
Test results include several ratings for each tractor. For comparative purposes, look at the figures that indicate tractor PTO horsepower and specific fuel consumption at maximum PTO horsepower. The next step is to test the tractor.
The tractor should be tested on a certified PTO dynamometer found at most equipment dealers. Attach the tractor’s power take-off to a dynamometer, warm the engine up and check to see if it produces rated PTO horsepower. If tractor power is down by more than 5 percent, adjustments or a tune-up is needed. A tune-up may include changing air and fuel filters, cleaning and adjusting fuel injectors, and adjusting engine timing.
Another important part of tractor operation is checking fuel efficiency. This can be done at the time the tractor is operating on the PTO dynamometer. After the tractor is warmed to operating temperatures, stop the tractor and fill the fuel tank completely full. Operate the tractor at rated speed and load for 30 minutes (longer for more accurate results), then stop the tractor and refill the tank to the previous level, keeping track of the gallons needed. Fuel efficiency will give an idea of the engine’s condition.
Specific fuel consumption or fuel economy is measured in horsepower-hours per gallon (hp-hr/gal), much as automobile fuel efficiency is measured in miles per gallon. To calculate the efficiency of the tractor, first determine the gallons of fuel used in one hour. For example, a diesel tractor producing 155 hp and using 5.5 gallons in 30 minutes would use 11 gallons in an hour. Divide the 155 horsepower by 11 gal/h.
Compare this figure to University of Nebraska Tractor Test data during the PTO tests at rated horsepower. If the current efficiency is 5 to 10 percent less than original, there may be a problem that needs correction. If an engine is showing a 5 percent reduction in fuel efficiency, it is wasting about 5 percent of the fuel. In a 155 horsepower tractor burning 11 gal/hr, this adds up to 0.55 gallons of fuel wasted every hour or 275 gallons wasted every 500 hours of use. (see Predicting Tractor Fuel Use, for more details)
Avoid Modification of Tractor Engines
A tractor engine may be “modified” to get more power. Frequent claims about pulling bigger loads, getting new “life” from older models, and more power from new models are true. Engine modification can be done by several means. The most common is overfueling, while others include adding alcohol or LP gas injection, and turbo-charging naturally aspirated engines.
These all sound tempting when an operator is faced with covering more acres in less time. But are the consequences of boosting engine horsepower beyond original ratings worth it? The first problem is warranty. Most manufacturers do not allow any changes from standard specifications without voiding the warranty, so you’re on your own with the changes.
The second problem with engine modifications is an almost sure reduction in service life. Every machine design is a compromise. The designer must compromise between strength, reliability and cost to come up with a tractor rugged enough to do a job, but still meet an affordable price.
Power is a function of torque and RPM. Tractors are designed to operate at different travel speeds, but the final drives are not designed for all possible torques theoretically available. If power is increased 20 percent on a tractor, you’re assuming the manufacturer built the engine parts, clutch, transmission and final drive 20 percent stronger than originally needed. Speed also has an effect on service life. For the example just stated, the 20 percent increase of power could be used by keeping the tractor weight the same and travel faster. This would reduce the life of the transmission by about 15 percent. Conversely, if one uses the 20 percent additional power for 20 percent larger pulls and drives at a slower speed, the transmission life is reduced by 50 percent. Usually, to take advantage of the increased pulling ability, more ballast (weight) must be added to maintain effective traction. Then, all parts will be overloaded, and service life will suffer (Figure 2). In the end, the tractor probably will end up in the repair shop long before it should.
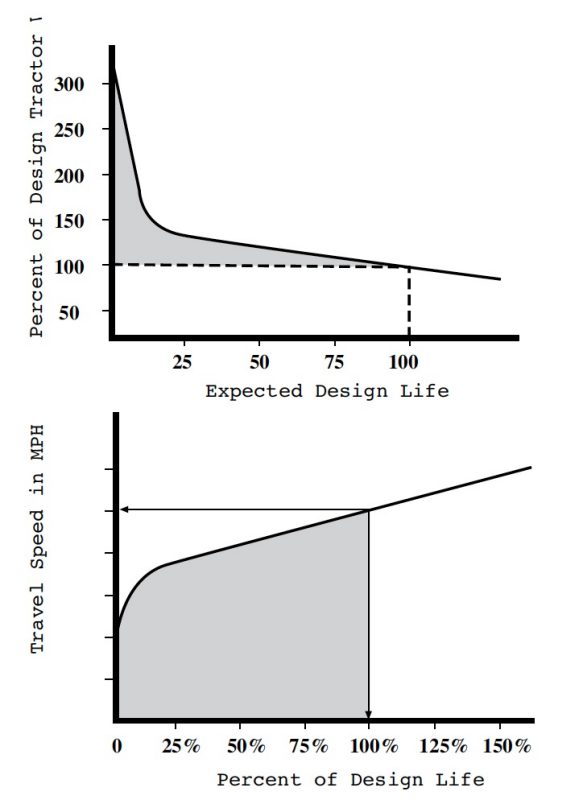
Changing the injector pump can be the simplest, cheapest and easiest engine modification. By pumping in more fuel (overfueling), the power of the engine will probably go up, but another problem arises. At the factory, most tractors are set to their most efficient operational level. If the engine is over-fueled, the fuel efficiency will decrease. This means the power output for the fuel poured into the engine will be less, so in the long run, the extra fuel will cost money.
If more power is needed, it is better, financially, to trade for a bigger tractor. Larger tractors are built for higher power from the radiator to the wheels and should give good service. Trying to get more power by modifying a tractor may prove to be extremely expensive.
Summary
This publication has discussed five strategies to achieve maximum life from farm machinery. These practices included machinery maintenance, oil analysis, machinery storage, engine tune-ups, and avoiding modifying tractor engines. No single item will have a large effect, but a combination of practices can have a large impact on costs, improve machine reliability for many years to come, and improve profit margins.
Also Review:
“Gear Up and Throttle Down” -- Saving Fuel. Virginia Cooperative Extension Publication 445-450.
Predicting Tractor Diesel Fuel Consumption. Virginia Cooperative Extension, Number 442-073.
Using Tractor Test Data for Selecting Farm Tractors. Virginia Cooperative Extension, Number 442-072.
Acknowledgments
The author would like to express his appreciation to former coauthor, Robert Pitman, for his input in previous versions.
Modified from Extend machinery life to save dollars. AE-939, North Dakota State University, Cooperative Extension Service, Fargo, ND.
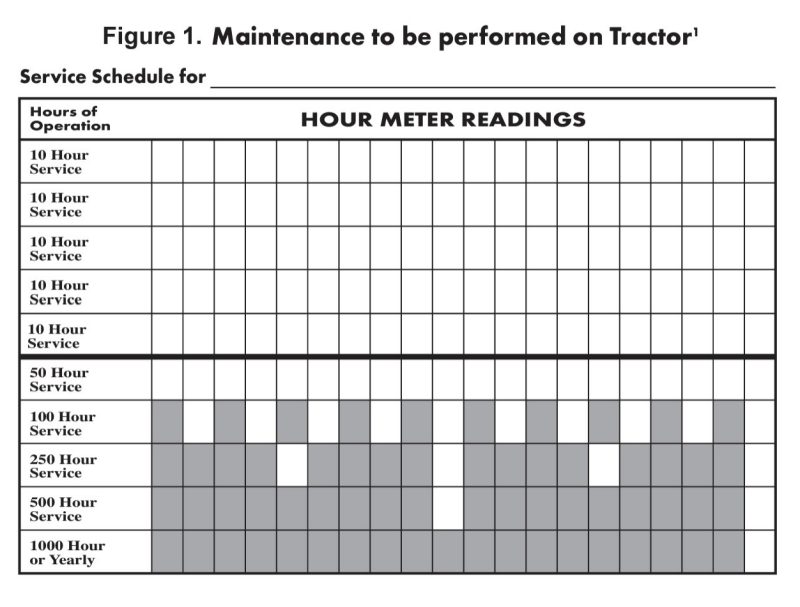
Maintenance as Required
Check Inflation Pressure
Adjust Brakes
Clean Cab Air Filter
Tighten Loose Nuts or Bolts
Repair Worn or Damaged Parts
Adjust Headlights
Remove Grease, Chaff and Soil
10 Hours (Daily)
Check Air Cleaner/Pre-cleaner
Check Crankcase Oil Level
Check Cooling System Level
Lubricate Grease Fittings
Check Fuel Sediment bowl
Check for Loose or Damaged Parts
Check for Leaks
Check for Drive Belts and Hoses
50 Hours (Weekly)
Check Battery Electrolyte Level
Check Hydraulic System Fluid Level
Check Transmission Oil Level
Clean Dry-Element Air Cleaner
Check Inflation Pressure
Perform 10-Hour Maintenance
100 Hours (Every 2 Weeks)
Change Crankcase Oil and Filter
Perform 10 and 50-Hour
250 Hours (Monthly)
Clean Battery
Adjust Clutch Pedal Free Travel
Check Belt Tension
Check and Adjust Brakes
Perform 10 and 50-Hour Maintenance
500 Hours (Every 2 Months)
Replace Fuel Filter
Perform 10, 50, 100 and 250-Hour Maintenance
1000 Hours (Yearly)
Drain and Refill Transmission Maintenance and Hydraulic System
Adjust Engine Governor if Recommended by Manufacturer
Clean and Repack Front Wheel
Drain, Clean, and Refill Cooling System
Check Air Conditioning Components
Perform 10, 50, 100, 250, and 500-Hour Maintenance
1 Always follow the Operator's Manual Recommendations, as particular maintenance operations will vary with make and type of implement.
Virginia Cooperative Extension materials are available for public use, reprint, or citation without further permission, provided the use includes credit to the author and to Virginia Cooperative Extension, Virginia Tech, and Virginia State University.
Virginia Cooperative Extension is a partnership of Virginia Tech, Virginia State University, the U.S. Department of Agriculture, and local governments. Its programs and employment are open to all, regardless of age, color, disability, sex (including pregnancy), gender, gender identity, gender expression, genetic information, ethnicity or national origin, political affiliation, race, religion, sexual orientation, or military status, or any other basis protected by law.
Publication Date
May 13, 2020