Understanding Spray Tank Mixing Practices
ID
BSE-351P
EXPERT REVIEWED
Introduction
Mixing two or more pesticide products can allow for the treatment of multiple pests at the same time, improve pesticide performance, and ultimately save time and money. However, physical and chemical tank mix incompatibilities can occur when combining two or more pesticides. Physical incompatibility is the failure of pesticide products to stay uniformly mixed and can include oil- and water-based products separating into layers, products falling out of solution as solids, gels, or pastes, or coagulating into clumps that can clog spray nozzles (Whitford et al. 2014). Chemical incompatibility occurs when an undesirable chemical reaction takes place by mixing two or more products together (Kentucky Pesticide Safety Education 2018). Indications of chemical incompatibility can be heat, strong odors or gas, or color change, and can render a pesticide ineffective (Whitford et al. 2014). Checking product compatibility prior to mixing can prevent loss of pesticide products and lost time to clean out sprayers (Whitford et al. 2018). This publication focuses on basic factors that influence physical product compatibility and summarizes best mixing practices.
The primary factors affecting pesticide mixing (fig. 1) include
- Agitation speed and method
- Water temperature and quality (e.g., hardness, pH)
- Mixing order
- Carrier type (water, oil, or fertilizer)
- Chemical formulations
Always carefully read product labels for specific tank mixing recommendations or protocols.
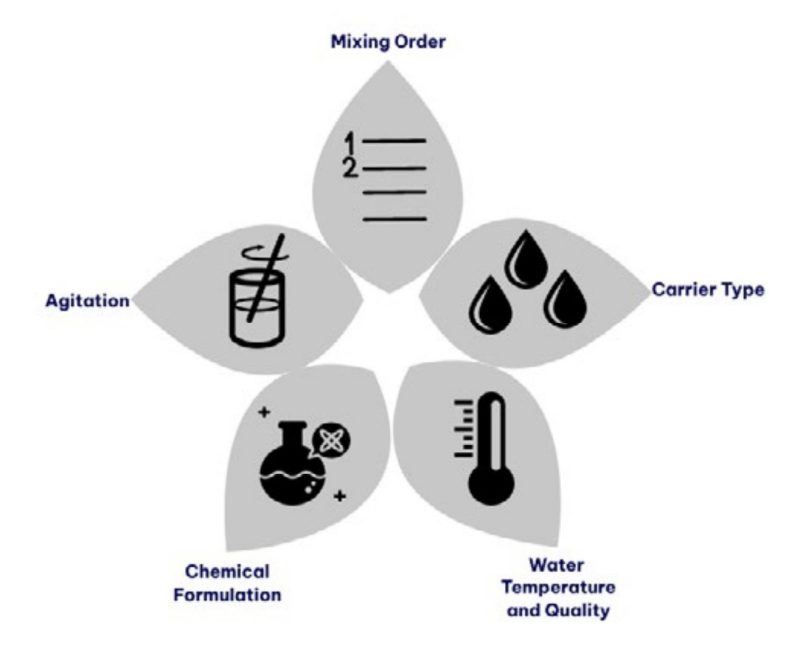
Agitation Speed and Method
Agitation is defined as shaking or stirring to achieve a uniformly mixed solution. The rate of agitation of certain products and the amount of time between adding more products affects successful pesticide mixing. Agitation can be influenced by water temperature, carrier type, and the volume of water or fertilizer in the tank. The tank mix should be agitated between the addition of each product in the tank. Without sufficient agitation, the pesticide product may separate and form layers (Whitford et al. 2014). In general, allow at least 3-5 minutes for a product to fully mix before incorporating additional products to the tank (Whitford et al. 2014). Some products, such as wettable powders (WP), water dispersible granules (WDG), suspension concentrates (SC), and emulsifiable concentrates (EC) will settle out over time and may require additional agitation during spray application.
Over-agitating or agitating too aggressively can also impact the mixing process, resulting in foaming or clumping (fig. 2), reducing the uniformity of the mix (Whitford et al. 2018). Providing moderate agitation of the spray mix, where movement of the spray solution at the top of the tank is apparent, will ensure all products are dispersed. If the spray mixture looks like boiling water, the agitation is too aggressive (Whitford et al. 2018).
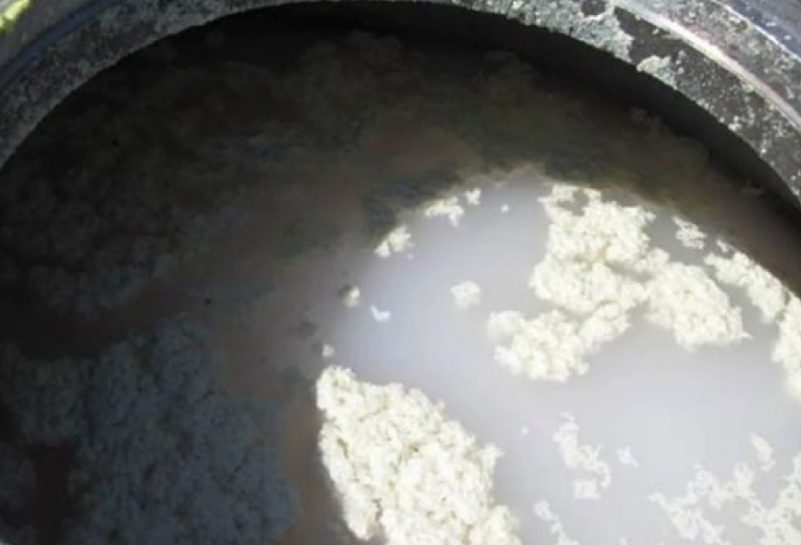
Water Temperature and Quality
Water temperature can influence the rate at which pesticides dissolve, disperse, and, ultimately, perform. Most pesticides more easily dissolve and/or disperse Water temperature is not something that can always be easily manipulated, so if cold water temperatures are unavoidable, be prepared to increase the mixing time or choose a pesticide formulation less sensitive to water temperature extremes. Always pay attention to product labels, as they will specify any sensitivities to extreme water temperatures.
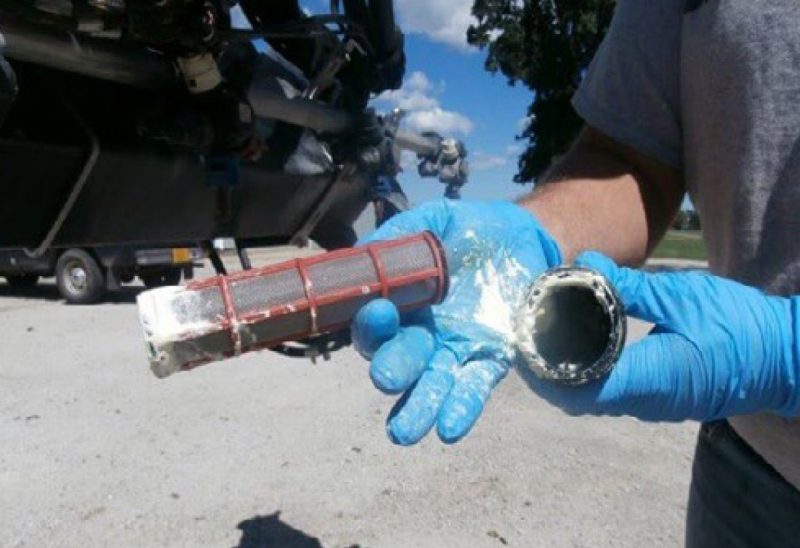
Mixing Order
The order in which pesticide products are introduced to the spray tank can affect the ability of the carrier to disperse suspended material (Whitford et al. 2014).
Mixing in the wrong order can lead to incompatibilities, which can adversely affect water pH and the solubility and mixing potential of products (Whitford et al. 2014). Incompatibilities will almost always result in reduced pesticide efficacy. Make sure to read all product labels, as they often state the recommended mixing order. If the mixing order is not stated, add pesticides to the tank using the WALES/DALES method (fig. 4). This method is a simplified process for understanding mixing order to avoid problems from mixing issues if instructions are not available on the label: W stands for wettable powders (D for dry formulations), A for agitate (in between each new product), L for liquid flowables, E for emulsifiable concentrates, and S for surfactants or adjuvants (fig. 4). Always consider the carrier type to lower the risk of incompatibilities.
W.A.L.E.S/ D.A.L.E.S Method For Mixing Pesticides
- Make sure to read alll labels before starting the mixing products and consult your manufacturer if you have any questions
- Shake all containers with liquids before adding to ensure smooth mixing
- Fill the spray tank with 50% of the required water volume before adding formulations
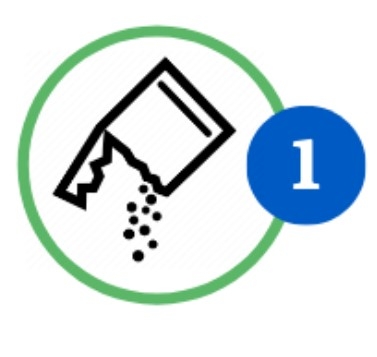
WorD
Dry formulations {DF) should be added to the tank.first. This includes wettable powders (WP/W), water dispersible granules (WDG), and water soluble packets (WSP). Make sure these products have fully dissolved before moving to the next step.
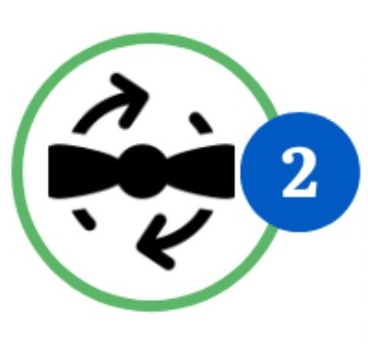
A
Agitation should be continuous throughout the mixing process, starting when the tank. is half full and continuing after adding each product until the end.
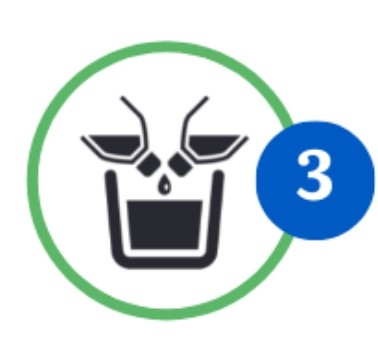
L
Add l1iquid (L), flowable IFJ, and soluble concentrate (SC) formulations next.
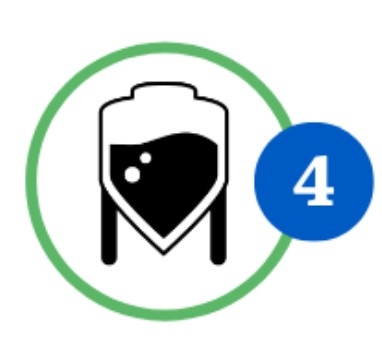
E
Emu lsifiable Concentrates (EC) should be added next, and Microencapsulated (ME) formulations should follow after that.
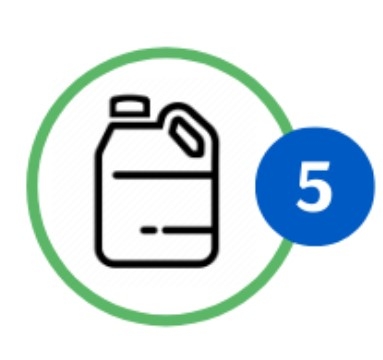
s
Surfactants and other adjuvants can be added last This includes drift control agents, crop oils, etc. The final step is to fill the tank with the remainder of the needed water and continue agitation.
Carrier Types
The two most common carriers used to mix pesticides are water and liquid fertilizers. Water is the primary carrier for pesticide applications and in many cases is a more effective carrier than liquid fertilizer because most products are created to be used with water (Whitford et al. 2018). Pesticide applicators draw from a variety of water sources for their sprays, including wells, surface water like streams or ponds, and municipal water, which may have differing water quality that can affect pesticide performance. Applicators should test all of their spray water sources for pH, hardness, mineral content, and other characteristics (Whitford et al. 2018). To learn more about water quality testing and understanding water test results, see Virginia Tech publication BSE-350P, “Spray Water Quality and Pesticide Characteristics.”
When using water as a carrier, lower the risk of incompatibilities by filling the spray tank with at least 50% of the required volume of water before adding products. When using liquid fertilizers as a carrier, fill the tank to 50%-75% of the required volume prior to adding products (Whitford et al. 2018). The more products you add to a liquid fertilizer solution, the greater the risk for incompatibilities (Whitford et al. 2018). Liquid fertilizers often have high salt content and dissolve less product than water (Whitford et al. 2018). In some instances, products should be mixed in water first, then added as a pre-slurry to the liquid fertilizer carrier to prevent incompatibilities. Dry product formulations such as water dispersible granules (WDG) do not fully disperse in liquid fertilizers (Whitford et al. 2018). Always pay attention to compatibility and mixing order when substituting water with liquid fertilizer.
An exception to the use of water or liquid fertilizer as a carrier is when using some oil-soluble pesticides, such as basal bark herbicides. In these cases, the product may need to be mixed with an oil carrier for final application. The oil carrier enhances the activity of the pesticide by increasing absorption into plant tissue, increasing wetting and spreading of the product, and improving rain fastness. To ensure a pesticide is dispersed effectively, always use the recommended carrier listed on the pesticide label.
Chemical Formulations
A pesticide formulation is a combination of active and inactive (inert) ingredients that form a pesticide product (Virginia Cooperative Extension 2020). The active ingredient is the substance in the pesticide intended to control a target pest. Inert ingredients do not have any pesticidal activity. They are added to dilute the active ingredient, reduce toxicity, and make the pesticide safer to use and easier to handle (Virginia Cooperative Extension 2020). Pesticide active ingredients vary in their physical and chemical properties and require different levels of agitation, temperatures, and carriers (Virginia Cooperative Extension 2020). Some pesticide products may also require the addition of an adjuvant prior to use. Adjuvants are chemicals added to a pesticide mixture to improve mixing, application, or efficacy of the active ingredient. Adjuvants may already be included in the formulation, or they may be added separately into a tank mix prior to use. For a detailed explanation of pesticide chemical formulations, see Unit 4, Pesticide Formulations, in the “Virginia Core Manual: Applying Pesticides Correctly,” publication 456-210, available for purchase from Virginia Cooperative Extension (https://vtpp.ento.vt.edu/index/manuals.html).
Testing Compatibility
To evaluate compatibility before mixing in the spray tank, especially if mixing unfamiliar products, conduct a jar test first. A jar test can reveal physical
incompatibilities in mixing such as settling, separation, gelling, sludge development, oil residue buildup, floating particles on the surface, and precipitation. A jar test can also reveal chemical incompatibilities, often signified by heat or strong odors (Whitford et al. 2014; Whitford et al. 2018). Read the product label to determine the mixing order for a jar test and always follow this order. If the label does not have the recommended mixing order on it, here are the general steps:
- Fill a jar half full with water or other carrier such as fertilizer.
- Add products in proportion to the tank mix, one at a time, in the proper order following the labels’ instructions or the WALES/DALES method.
- Shake the jar between each addition and allow it to stand for 10-15 minutes.
- Look for signs of incompatibility (fig. 5). Products that are incompatible will separate into layers, create clumping or foam, give off heat, or precipitate.
- If physical incompatibility is observed, begin the process over again. Consider adding a compatibility agent this time. If physical incompatibility is still an issue, you may need to replace one or more of the pesticides with a differ- ent product (Weisbrod and Puckett, 2023).
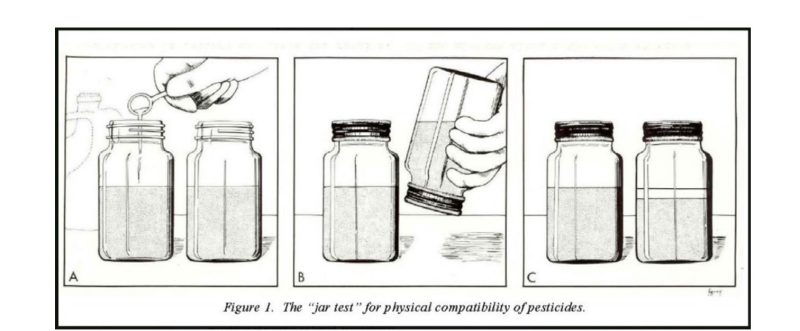
Label Warnings
Always read the pesticide product labels thoroughly and consult a pesticide dealer, Extension agent, and/ or manufacturer before adding an unfamiliar product or adjuvant to a spray mix, especially if water pH or temperature is out of the preferred range. Using the wrong tank mix can be harmful to crops or equipment. Some label warnings to be aware of include
- Mixing order.
- Compatibility of spray products.
- Recommended carrier “source” and volume.
- Need for adjuvant.
- Warnings about spray water pH or mineral content.
- Sensitivities to extreme temperatures.
Labels may or may not specify the recommended tank-mixing practices. For more information on the use of adjuvants to improve pesticide mixing, other recommendations, and warnings about pesticide products, see Virginia Tech publication BSE-352P, “Solving Spray Water Problems,” available on the Spray Water Analysis Program web page (https://www. wellwater.bse.vt.edu/swap).
Conclusion
It is important to understand pesticide products when mixing to avoid incompatibility and solubility problems and to prevent damage to crops and equipment. Using the WALES/DALES method can help avoid tank mixing issues. Conducting a jar test can help producers make sure products are compatible without wasting large amounts of product. The more products being mixed, the greater the risk for incompatibility. Plan ahead of time to avoid problems and delays of spray application. Always read product labels carefully, which often specify mixing order, recommended temperature, suggested carrier type, pH, and the type of pesticide formulation.
References
Chahal, G., J. Roskamp, T. Legleiter, and B. Johnson. 2012. “The Influence of Spray Water Quality on Herbicide Efficacy.” Purdue Weed Science, Purdue University, West Lafayette, IN. https://ag.purdue.edu/btny/purdueweedscience/extension/water_quality/.
Kentucky Pesticide Safety Education. 2018. “Using Pesticide Formulations.” University of Kentucky, Lexington. https://www.uky.edu/Ag/Entomology/PSEP/3formulations.html.
Virginia Cooperative Extension, Applying Pesticides Correctly, Virginia Core Manual, 2020 https://vtpp.ento.vt.edu/index/manuals.html
Weisbrod, J. M. and G.J. Puckett. 2023. Testing Pesticide Mixtures for Compatibility, Nebraska Extension G2350. https://extensionpublications.unl.edu/assets/html/g2350/build/g2350.html
Whitford, F., G. Lindner, B. Young, D. Penner, J. Deveau, D. Linscott, and H. Zhu et al. 2014. “Adjuvants and the Power of the Spray Droplet.” Publication PPP-107. Purdue University Extension, West Lafayette, IN. https://ag.purdue.edu/department/extension/ppp/resources/ppp-publications/ppp-107.html.
Whitford, F., M. Olds, R. Cloyd, B. Young, D. Linscott, J. Deveau and J. Reiss et al. 2018. “Avoid Tank Mixing Errors: A Guide to Applying the Principles of Compatibility and Mixing Sequence.” Publication PPP-122. Purdue University Extension, West Lafayette, IN. https://ag.purdue.edu/department/extension/ppp/resources/ppp-publications/ppp-122.html.
Acknowledgements
The authors would like to acknowledge the following individuals who assisted with writing and editing this publication and the development of the Virginia Tech Spray Water Assessment Program: Asa Spiller, Research Analyst, Virginia Tech Biological Systems Engineering; Brian Benham, Professor and Extension Specialist, Virginia Tech Biological Systems Engineering; Kelly Peeler, Water Quality Lab Manager, Virginia Tech Department of Biological Systems Engineering; Jeffrey Parks, Virginia Tech Department of Civil and Environmental Engineering; Michael Heatwole, Virginia Water Well Association and WaterRight ™. Thank you to the following Virginia Cooperative Extension agents, who were instrumental in creating the Virginia Tech Spray Water Assessment Program: Mark Sutphin, Timothy Ohlwiler, Ashley Edwards, Ashley Appling, Beth Sastre-Flores, Laura Maxey Nay, Ed Olson, Scott Reiter, Stephanie Romelczyk, and Jason Cooper.
Virginia Cooperative Extension materials are available for public use, reprint, or citation without further permission, provided the use includes credit to the author and to Virginia Cooperative Extension, Virginia Tech, and Virginia State University.
Virginia Cooperative Extension is a partnership of Virginia Tech, Virginia State University, the U.S. Department of Agriculture, and local governments. Its programs and employment are open to all, regardless of age, color, disability, sex (including pregnancy), gender, gender identity, gender expression, genetic information, ethnicity or national origin, political affiliation, race, religion, sexual orientation, or military status, or any other basis protected by law.
Publication Date
February 22, 2024