Soil Moisture Sensors for Agricultural Irrigation: An Overview on Sensor Types
ID
BSE-338P
EXPERT REVIEWED
Irrigation can be a crucial part of avoiding crop losses and improving yields. However, to obtain the best agronomic and financial results, irrigation should be scheduled in a way that prevents crop water stress while also avoiding overwatering. Irrigation scheduling is the practice of determining when to irrigate and how much water to apply. If too much time passes between irrigation events, plants can experience water stress, poor growth, and low yields. On the other hand, when too much irrigation is applied, water will run off fields or percolate down below the root zone. This leads to excessive pumping costs and the loss of nutrients applied to the field. It also has negative environmental impacts, since excess water is used, and leached nutrients can harm surface and groundwater quality.
Monitoring soil moisture content can support irrigation scheduling by telling you how much water is present in your soil at any time. Irrigation should be applied when soil moisture levels drop below a minimum threshold. While the benefits of irrigation are most obvious in dry years, scheduling irrigation can improve yields in wet years as well by providing water when the timing or amounts of rainfall are not optimal. For instance, in six years of experiments on peanut yields under different irrigation treatments in Georgia, scheduling irrigation with the aid of soil moisture sensors consistently resulted in higher yields that often outperformed other irrigation scheduling methods (table 1). However, it is important that soil moisture sensors are selected, installed, and used appropriately to obtain the most benefit.
Year | Rainfall (inches) |
Dryland Yields (lb/acre) |
Sensor Yields (lb/acre) |
Checkbook Yields (lb/acre) |
---|---|---|---|---|
2014 | 12.3 | 465 | 6,052 | 5,025 |
2015 | 22.7 | 5,194 | 5,479 | 5,313 |
2016 | 25.8 | 5,249 | 6,292 | 6,367 |
2017 | 24.3 | 5,875 | 6,396 | 5,749 |
2018 | 32.7 | 5,491 | 6,047 | 5,650 |
2019 | 19.7 | 5,874 | 7,076 | 6,607 |
The goal of this publication is to provide an overview on different methods for monitoring soil moisture content in agricultural settings and for obtaining the data provided by soil moisture sensors. This publication complements other Virginia Cooperative Extension publications.
For example, VCE publication BSE-239P, “Irrigation Scheduling in Humid Climates Using the Checkbook Method” (Shortridge 2018), describes how to schedule irrigation when soil moisture data are unavailable.
VCE publication BSE-339P, “Scheduling Agricultural Irrigation Based on Soil Moisture Content: Interpreting and Using Sensor Data” (Shortridge and Porter 2021), provides an overview on how to use data from soil moisture sensors to schedule irrigation. And VCE publication BSE-198P, “Understanding Soil Moisture Sensors: A Fact Sheet for Irrigation Professionals in Virginia” (Sample et al. 2016), provides details on different types of soil moisture sensors and how they can be used in irrigation, with a focus on landscape applications.
This publication assumes that the reader is familiar with basic soil water concepts such as field capacity, permanent wilting point, and plant-available water. More information on these topics is presented in VCE publication BSE-239P (Shortridge 2018). The first section of this publication provides discussion on different methods for monitoring soil moisture levels and plant water stress, including manual inspection, soil moisture sensors, and remote sensing. The second section describes different methods for obtaining data from these sensors, including manual reading and remote data services. By reading this document, irrigators and educators should gain a better understanding of different options for soil moisture monitoring and which methods might be most appropriate for their needs.
Sensing Methodologies
Multiple methods are available for measuring soil moisture content, each of which differs in terms of cost, accuracy, and required technical knowledge. The following sections discuss different sensing methods, including manual soil inspection, tensiometers, electrical resistance (tensiometric) sensors, volumetric water content sensors, and remote sensing. While these sections provide general information about the different type of sensors, individual models may vary in terms of their cost, accuracy, installation procedures, and calibration requirements. To achieve the best performance, it’s crucial to follow manufacturer instructions regarding the installation, calibration, and use of any sensor.
Manual Inspection
The look and feel of the soil can provide a lot of information about its water content. The advantage of using manual inspection to estimate soil moisture content is that it is easy to use and does not require expensive equipment. The disadvantage is that the accuracy is generally low (although experience using this method can improve accuracy) and fieldwork is needed to collect the soil samples. While soil inspection can provide some insight into whether irrigation is necessary, it won’t tell you how much water to apply unless you also inspect the soil immediately after irrigating.
Soil samples should be collected from about 6-12 inches below the ground surface from several sites across the field that are representative of the field’s main soil type. Hold the soil sample in your hand and try to squeeze the soil into a ball. For medium- and fine-textured soils (loams and clay loams), you can press the soil between your thumb and forefinger to attempt to form a ribbon, and rub the soil between your thumb and forefinger to see if it feels slick when rubbed. Table 2 presents a summary of how different soil types look and feel at different levels of plant available water. Additional details on this method, including photographs demonstrating soil appearance at different soil moisture levels, are available in the USDA National Resource Conservation Service (1998) document “Estimating Soil Moisture by Feel and Appearance.”
Approximate plant- available water remaining in soil |
Soil texture coarse (loamy sand) |
Soil texture sandy (sandy loam) |
Soil texture medium (loam) |
Soil texture fine (clay loam) |
---|---|---|---|---|
100% (field capacity) |
Leaves wet outline on hand when squeezed | Very dark, leaves wet outline on hand | Very dark, leaves wet outline on hand, will ribbon out to about 1 inch | Very dark, leaves slight moisture on hand when squeezed, will ribbon out to about 2 inches |
75% | Appears moist, makes a weak ball | Quite dark color, makes a hard ball | Dark color, forms a hard or plastic ball, may slick when rubbed | Dark color, may slick when rubbed and forms ribbon |
50% | Appears slightly moist, slightly sticks together | Slightly to fairly dark, makes a ball | Slightly to fairly dark, forms a ball | Fairly dark, makes a good ball, may form thick ribbon and slick when rubbed |
25% | Appears to be dry, will not form a ball under pressure | Lightly colored, will not form ball | Lightly colored, small clods, crumbles fairly easily | Slightly dark, forms weak ball, small clods flatten rather than crumble |
0% (permanent wilting point) |
Dry, loose, grains will flow through fingers | Very slight color, loose, flows through fingers | Slight color, powdery, dry, sometimes slightly crusted but easily broken | Some darkness, hard baked, cracked, sometimes with loose crumbs on the surface |
Tensiometers
How They Work
A tensiometer consists of a water-filled tube with a ceramic tip and a vacuum gauge that measures soil water tension (fig. 1). Soil water tension is the pressure the plant must exert to remove water from the soil. In dry soil, water is “held” more tightly in the soil, requiring the plant to exert more energy. When the soil becomes wet, the soil water tension declines, meaning that it can be removed more easily by the plant. A tensiometer works by exchanging water with the surrounding soil through a porous ceramic tip that mimics a plant’s root. In dry soil, water is drawn out of the tensiometer, creating negative pressure or suction inside the tensiometer’s vacuum tube. As the soil becomes wet, water moves back into the tensiometer, and the negative pressure is reduced. Tensiometers typically measure pressure in centibars (cb) or kilopascals (kPa).
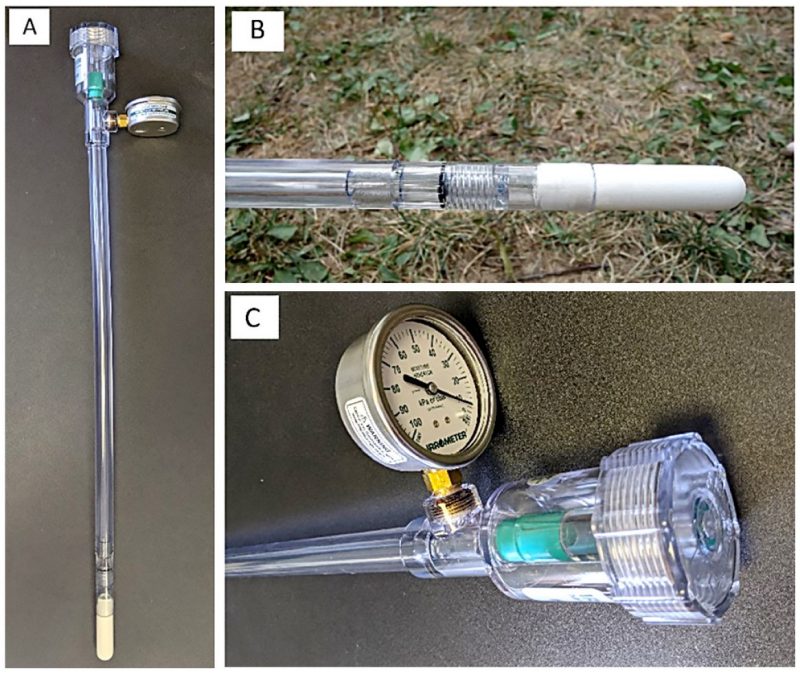
Advantages and Disadvantages
Because tensiometers measure soil water tension directly, they aren’t impacted by temperature or salinity and do not require calibration upon installation. They also do not require an electricity source. Most tensiometers read pressures between 0 and 100 cb (equal to 0 to 100 kPa). However, greater ranges may be necessary in heavy clay soils (where irrigation might not be triggered until the soil water tension is greater than 100 cb or 100 kPa). On the other hand, in very sandy soils and non-soil growing media, irrigation may be needed when the soil tension is comparatively low and can be better managed with low-tension tensiometers that read between 0 and 40 cb. It can be difficult to get accurate readings in soil that contains gravel or other aggregate material. The limit of accuracy of most tensiometers is around 80 cb, at which point the vacuum tension is likely to be broken. This is also the level at which water stress begins to occur for deep-rooted crops in medium- and fine-textured soils. Thus, tensiometers might not be suitable for applications where low levels of plant-available water are desired, such as deficit irrigation.
Installation, Calibration, and Maintenance Considerations
Tensiometers are typically installed by augering a hole into the soil that is the exact diameter and depth of the tensiometer. Because it is important that the diameter of the hole be the same diameter of the tensiometer, they are often sold with installation tools that ensure the correct hole diameter. Tensiometers can also be installed by augering a hole that is a larger diameter than the tensiometer, creating a slurry by mixing water with the removed soil, and putting some of this slurry back into the hole. The tensiometer is then placed with the tip in the slurry, and then the hole is backfilled with the removed soil. The borehole should be backfilled with the same soil removed from the hole and tamped down to prevent water from preferentially flowing down the backfilled borehole. Mound soil at the top of the installation to prevent water from pooling over the tensiometer.
Tensiometers may need to occasionally be refilled with water. Most tensiometers designed for long-term use have an external gauge and refill tube so they can be refilled without removing the tensiometer from the ground; however, models without this feature have to be removed. If tensiometers are allowed to dry out completely, they typically will require maintenance or repair, and they could be damaged if temperatures drop below freezing. Because of this, they should not be used in situations where soil regularly becomes very dry or where frost conditions are expected to occur.
Electrical Resistance Sensors
How They Work
Electrical resistance sensors (fig. 2) consist of two electrodes that are embedded in a block of granular material such as gypsum (they are sometimes referred to as granular matrix sensors or gypsum blocks). The granular matrix is placed directly in the soil and exchanges water with the surrounding soil like a tensiometer. As the soil dries, water is pulled out of the granular matrix sensor because of high soil water tension. As the soil becomes wet, soil water tension declines and water moves back into the sensor. The electrodes embedded in the granular matrix measure the electrical resistance of the granular material. Electrical resistance of the granular matrix varies depending on the water content in the sensor because water is a good conductor of electricity. As the sensor dries, the electrical resistance increases, and as the sensor gets wet, the electrical resistance decreases. The meter reading can be converted to an estimate of soil water tension in cb or kPa, similar to a tensiometer.

Advantages and Disadvantages
Electrical resistance sensors are typically one of the lowest cost options for measuring soil moisture content. They can be used in moderately saline soils and typically require very little maintenance. However, they are less effective in sandy soils because there is a time delay between when the soil dries and when the sensor dries. Because of this time delay, electrical resistance sensors are not recommended for vegetable production operations where short-cycle pulsing irrigation is used. The sensor response time is too slow to properly see the effects of the small, frequent irrigations. In addition, obtaining good soil contact can be challenging in sandy or gravely material.
Installation, Calibration, and Maintenance Considerations
Electrical resistance sensors are permanently embedded in the soil, and wires from the blocks are plugged into an aboveground meter for reading. Prior to installation, the sensors are typically soaked in water to remove air bubbles and improve accuracy. The sensors can be installed by boring a hole to the desired depth, making a mud slurry using soil removed from the hole, refilling the borehole with the slurry, and placing the sensor within the slurry with the wires rising out of the borehole. The wires should be encased in PVC or metal conduit to prevent damage. The borehole should be backfilled with the same soil removed from the hole and tamped down to prevent water from preferentially flowing through the backfilled borehole. Mound soil at the top of the installation to prevent water from pooling over the tensiometer.
Calibration requirements vary; some sensor models are designed to have a stable calibration that does not need to be repeated for different soil types as long as readings of soil water tension (rather than soil moisture content) are acceptable. Other models may require recalibration for different soil textures. The meters sometimes need to be recalibrated if they are allowed to completely dry out. When using electrical resistance sensors, be sure to follow the manufacture’s calibration procedures closely. Once the sensors are properly installed and calibrated, they typically require little maintenance; however, the buffering capacity of the gypsum is reduced, which requires replacement of the sensor every three to four years or a recalibration of the sensor.
Volumetric Water Content Sensors
How They Work
Multiple varieties of sensors (sometimes referred to more specifically as dielectric sensors, capacitance sensors, time domain reflectors, and amplitude domain reflectors) can be used to measure the volume of water in the soil. Soil is composed of solid materials (minerals and organic materials), air spaces, and water. Volumetric water content is the measure of the volume of water in a soil sample divided by the total volume of the soil sample. Volumetric water content varies by soil type. When saturated (all air spaces are filled with water), sandy soil may only contain 20-30% water by volume, whereas the volumetric water content of saturated clay can be 50%.
To estimate the volumetric water content of the soil, volumetric sensors measure various electrical properties of the soil, such as how well it can hold an electric charge or the speed at which an electromagnetic wave passes through the soil. Since water is a good conductor of electricity, these properties will change depending on the volume of water in the soil. Volumetric water content sensors measure these electrical properties and then use a soil-specific calibration equation to convert these measurements into volumetric soil content estimates. More details on specific varieties of volumetric water content sensors are provided in VCE publication BSE- 198P (Sample et al. 2016).
Advantages and Disadvantages
If properly calibrated, volumetric water content sensors are typically very accurate, respond quickly to soil wetting, are able to sense a wide range of soil moisture levels, and are generally suitable for use in saline soils. Some sensors can also measure other parameters, including soil temperature and electronic conductivity (which can be used to estimate salinity and nutrient levels), allowing additional information to be obtained from a single sensor. The prices of dielectric sensors can vary significantly depending on their specifications.
One challenge in the use of dielectric sensors is that they require soil-specific calibration. Manufacturers typically provide calibration procedures and equations, but the accuracy of these procedures may vary in practice. The volume of soil measured by these sensors varies, with more complex and expensive sensors measuring larger soil volumes. This type of sensor must be connected to an electricity source (usually a data logger is used for this purpose). Installation can be difficult in soils that contain gravel or other aggregate material.
Installation, Calibration, and Maintenance Considerations
Dielectric sensors are most commonly available in a pronged form, where two or three prongs are inserted into undisturbed soil (fig. 3). It is critical that these sensors are installed directly into undisturbed soil. To install pronged dielectric sensors, dig a borehole to the desired depth. As you are digging, place the excavated soil on a plastic tarp or bag so you can see if there is a change in material and return excavated soils to the appropriate depth (fig. 4). When the soil is backfilled, the deepest soil should be placed in the borehole first. The sensors should be firmly pressed into the bottom or sides of the borehole at the desired depth so that all prongs are completely inserted into the undisturbed soil. The sensor wires should be encased in hard conduit aboveground to avoid damage and to aid in sensor removal. The borehole should be backfilled so that soil is returned to the same depth it was removed from and compacted regularly to avoid preferential water flow above the sensor.
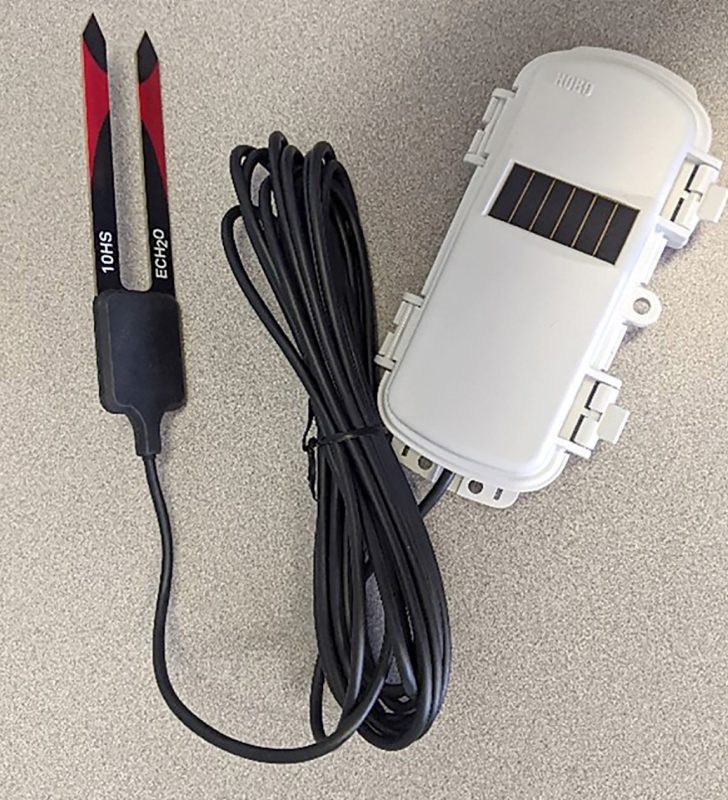

Portable capacitance sensors can also be used to measure volumetric water content. Capacitance sensors measure a profile of soil moisture content from the ground surface to a specific depth. Capacitance sensors are typically packaged in probes up to 1 meter long, with multiple stainless steel rings installed along the length of the probe. To use these probes, an access tube is semipermanently installed in the soil. While these types of sensors are typically more expensive, they have the benefit of providing measurements at multiple depths, and a single sensor can be used to obtain readings at multiple locations if additional access tubes are installed. The access tube is installed by augering a hole in the soil that is the same depth and a slightly larger diameter than the access tube. The access tube is then inserted into the augured hole and remains there until the end of the growing season. The probe can then be inserted into the access tube whenever a reading is desired or left in place for continuous monitoring.
Both volumetric and capacitance probes require calibration. Most manufacturers include standard calibration equations for different soil types. These equations can be used to convert the raw sensor output into a soil moisture content estimate, but they might not be accurate for a specific location. Better accuracy is possible by doing a site-specific calibration. A precise calibration requires removing soil samples and wetting them to a known soil moisture content, and then recording the resulting dielectric measurement. An in situ calibration can also be obtained by wetting the soil in place, observing soil moisture readings through time, and combining this with information about the soil type to identify field capacity and wilting point. Other than calibration, dielectric sensors typically require very little maintenance. However, if sensors are reused after a prior application, they should be cleaned using a mild soap prior to being reinstalled.
Remote Sensing
A final, rapidly developing approach for collecting data to aid in irrigation management is remote sensing. Remote sensing refers to the use of sensors that measure the condition of the soil and plants in a field without requiring physical contact or the collection of samples. Remote sensing includes everything from hand-held infrared thermometers (special cameras that can be permanently mounted in a field), to cameras mounted onboard unmanned aerial vehicles (UAV, also referred to as drones), and even measurements from satellites. The following sections describe canopy temperature and spectral reflection, two primary types of remote sensing data that can be used to identify crop water stress and aid in irrigation management.
Canopy Temperature
Canopy temperature refers to the temperature of a crop’s leaves. The process of evapotranspiration cools plants, so when evapotranspiration rates decline due to water stress, the plant’s temperature goes up. Canopy temperature can be measured remotely using sensors that measure infrared energy emitted by the canopy. All objects emit energy, and the amount of energy emitted increases as an object becomes warmer. Many commercially available sensors can be used to measure canopy temperature. These include infrared thermometers, which record a single reading of the temperature, and infrared thermal cameras, which measure temperature across their field of vision and record an “image” where each pixel is a temperature measurement.
Multiple factors influence canopy temperature, including ambient air temperature, cloud cover, and the position of the sun. Because of this, canopy temperature measurements have to be converted into an estimate of crop water stress to be useful for irrigation scheduling. Multiple methods can be used to translate canopy temperature into crop water stress. For example, the Crop Water Stress Index (CWSI) compares the difference between canopy and air temperature for well-watered and water-stressed vegetation. Indices such as Degrees Above Non-Stressed and Degrees Above Canopy Threshold have also been developed and have the advantage of requiring less data than CWSI. The accuracy of these methods is likely to vary depending on the crop being grown, cloud cover, time of day, time of year, and irrigation method employed (Kullberg, DeJonge, and Chavez 2017). Additional information on using infrared temperature measurement for irrigation is available in Nebraska Extension publication “Ground-Based Thermal Sensing of Field Crops and Its Relevance to Irrigation Management” (Lo et al. 2018).
Spectral Reflectance
Spectral reflectance refers to the wavelengths of light that a surface either absorbs or reflects. Spectral reflectance can be used to identify water stress in plants because vegetation absorbs and reflects light differently depending on whether the plant is stressed and to what degree. Spectral reflectance measurements are typically used to calculate an index value that can be related to plant water stress. The most common index is the Normalized Difference Vegetation Index. The NDVI is calculated by comparing the percentage of visible and infrared light that is absorbed and reflected by the plant because healthy, green vegetation absorbs more visible light and reflects more infrared light than unhealthy, sparse or browning vegetation. However, the primary limitation of using NDVI is that differences typically become apparent only after a plant is already visibly stressed. Because of this, other indices, such as the Photochemical Reflectance Index, are aimed at identifying plant stress earlier (Ihuoma and Madramootoo 2017). NDVI can be measured using hand-held sensors or cameras mounted on stationary positions above a field or on UAVs.
Just as with canopy temperature, vegetation indices have to be converted into an estimate of crop water stress or crop water use to be useful for irrigation scheduling. Prior research has found that NDVI can be used to estimate evapotranspiration (Stone and Bauer 2018; Hunsaker et al. 2003) and schedule irrigation using a checkbook method or another, similar water balance approach. For more information on using crop evapotranspiration estimates for irrigation scheduling, see VCE publication BSE-239P (Shortridge 2018).
Practical Considerations, Advantages, and Disadvantages
Remote sensing of canopy temperature or spectral reflectance can be implemented in multiple ways. Hand- held sensors are available that measure both canopy temperature and spectral absorption/reflectance. These devices are a low-cost and fairly straightforward way for implementing remote sensing but typically only provide readings over short distances and small areas.
They require traveling to different sections of the field and manually recording readings. Stationary infrared sensors and cameras can also be installed in fields for continuous readings and oriented so they measure temperature or spectral reflectance over a larger area, although this is typically over no more than a few square yards. Infrared and spectral absorption cameras can be mounted on UAVs and flown over a field to provide measurements across an entire field. The key advantage to this approach is that it can identify differences in conditions across a field that are unlikely to be apparent when using soil moisture sensors that only measure conditions in a small area. This can be useful for large fields where direct observation of different areas is costly and time-consuming.
A key challenge in implementing remote sensing is the degree of knowledge and technical capacity needed to translate sensor measurements into data useful for making irrigation management decisions. Infrared and spectral cameras, especially when mounted on UAVs, generate large volumes of data that require specialized knowledge and software to process, making them difficult to implement independently. Thus, using UAVs to collect and apply remotely sensed data for irrigation management often requires purchasing a service from a commercial provider. Regularly using such a service for irrigation scheduling is likely to be cost-prohibitive. However, even a small number of aerial thermal or spectral images can be useful in identifying field locations that might require more intensive management.
For instance, images could be used to identify areas that tend to dry out quickly, which can help in choosing locations for soil moisture monitoring using traditional sensors. Images can also identify problems such as locations where plugged or damaged irrigation nozzles are not applying the appropriate amount of water. However, there are multiple factors that can lead to high canopy temperature or unhealthy vegetation indices, including disease, nutrient deficiencies, and compacted soil. Thus, field scouting is still recommended to identify the underlying problem.
While research studies have shown that remotely sensed canopy temperatures and vegetation indices can accurately diagnose water stress and support irrigation management of certain crops and growing conditions, they have yet to be demonstrated on a broad scale or used widely in practice for irrigation scheduling. However, advances in sensing technology and data analysis methods, combined with decreasing costs as sensors and unmanned aircrafts become more common, could make these approaches more feasible for irrigation scheduling (and crop management more generally) in coming years.
Data Retrieval
Depending on the type of sensing technology used, different options are available for retrieving and viewing the data collected by the sensors. Some soil moisture and water potential sensors require manual reading. For instance, tensiometers are sometimes equipped with an analog vacuum gauge (shown in fig. 1), and some electrical resistance and volumetric water content sensors can be connected to a meter to collect instantaneous readings. The primary advantage of manual data collection is that it is comparably low-cost and simple to do. However, it requires more labor than other data retrieval methods since it requires traveling to the sensor location each time a reading is needed. This can be particularly time-consuming in large fields or if multiple sensors need to be checked. An additional limitation is that readings only provide a snapshot of conditions at that point in time, so it is not possible to see how soil moisture changes through time without repeatedly checking and recording sensor readings. To use sensor readings for irrigation management, sensors should be checked frequently to ensure that soil moisture levels do not drop below a predetermined soil moisture threshold.
Data loggers are computer systems that record sensor measurements at regular intervals. The main advantage of using data loggers is that they provide data on soil moisture conditions through time, rather than a snapshot or single point in time. This can be useful in determining how long it takes for soil to dry out after irrigation or how much water is needed to reach field capacity. A recording of sensor readings through time can also make it easier to spot errors or problems with the sensor. For instance, a sensor with poor soil contact may lead to erratic readings that can be difficult to identify if sensors are only checked occasionally. Some data loggers provide a display of current readings, but obtaining the full record of readings requires connecting the data logger to a computer and saving the data. Many data loggers can accommodate multiple sensors, so they can store measurements from multiple soil sensors installed at different depths or be combined with weather monitoring equipment. However, data loggers are more expensive than manual reading devices.
Many data loggers are now designed so that the recorded data can be sent via cellular, Bluetooth, Wi-Fi, radio, or even satellite communication systems, meaning that data can be collected and viewed without physically traveling to the sensor location. Multiple sensors can be connected together for whole field monitoring, where a central data logger communicates remotely with wireless sensors (fig. 3). This type of arrangement can be a convenient way to obtain data from multiple locations without purchasing numerous data loggers, which are often more expensive than the sensors themselves. The data can then be sent to a nearby computer or online data hosting services. Many commercial vendors that sell soil moisture sensors also provide data services where the data is automatically uploaded and available for viewing online without the need for programming or specialized software. This is a very convenient way of monitoring soil moisture conditions, particularly in large fields with multiple sensors. The primary downside is cost. In addition to purchasing a data logger with communication capabilities, it also typically requires paying a recurring fee for data retrieval and processing. Furthermore, not all data communication services are appropriate in all locations. For example, cellular data collection services require consistent cellular network coverage in the sensor location, which may not be available in some rural areas.
Conclusions
Properly scheduling irrigation is an important step in making sure that plants have sufficient water while also avoiding the excess costs, nutrient losses, and environmental impacts associated with overwatering. Monitoring soil moisture conditions can inform irrigation scheduling by helping producers know when to irrigate and how much water to apply. Many different sensing methods are available to aid in irrigation scheduling, ranging from manual field inspection to remote sensing. While these methods vary in terms of their cost, accuracy, and ease of use, all of them can be helpful in allowing the producer to manage their irrigation system more effectively. This can ultimately help growers improve yields without excess costs or environmental harm.
References
Hunsaker, D. J., P. J. Pinter, E. M. Barnes, and B. A. Kimball. 2003. “Estimating Cotton Evapotranspiration Crop Coefficients With a Multispectral Vegetation Index.” Irrigation Science 22:95-104.
Ihuoma, S. O., and C. A. Madramootoo. 2017. “Recent Advances in Crop Water Stress Detection.” Computers and Electronics in Agriculture 141:267- 75.
Lo, T. H., D. R. Rudnick, Y. Ge, D. M. Heeren, S. Irmak, J. Burdette Barker, X. Qiao, and T. M. Shaver. 2018. Ground-Based Thermal Sensing of Field Crops and Its Relevance to Irrigation Management. NebGuide 2301. University of Nebraska-Lincoln Extension. Lincoln: University of Nebraska Extension. https://extensionpublications.unl.edu/assets/pdf/g2301.pdf.
Kullberg E. G., K. C. DeJonge, and J. L. Chávez. 2017. “Evaluation of Thermal Remote Sensing Indices To Estimate Crop Evapotranspiration Coefficients.” Agricultural Water Management 179:64-73.
National Resources Conservation Service. 1998. Estimating Soil Moisture by Feel and Appearance. Washington, DC: NRCS. www.nrcs.usda.gov/Internet/FSE_DOCUMENTS/nrcs144p2_051845.pdf.
Sample, D. J., J. S. Owen, J. S. Fields, and S. Barlow. 2016. Understanding Soil Moisture Sensors: A Fact Sheet for Irrigation Professionals in Virginia. VCE publication BSE-198P. Blacksburg: VCE. https://ext.vt.edu/content/dam/pubs_ext_vt_edu/BSE/BSE-198/BSE-198-PDF.pdf.
Shortridge, J. 2018. Irrigation Scheduling in Humid Climates Using the Checkbook Method. VCE publication BSE-239P. Blacksburg: VCE. https:// pubs.ext.vt.edu/BSE/BSE-239/BSE-239.html.
Shortridge, J., and W. Porter. 2021. Scheduling Agricultural Irrigation Based on Soil Moisture Content: Interpreting and Using Sensor Data. VCE publication BSE-339P. Blacksburg: VCE.
Stone, K. C., and P. J. Bauer. 2018. “Variable Rate Irrigation Management Using NDVI.” Paper from the 14th International Conference on Precision Agriculture. International Society of Precision Agriculture. Montreal. June 2018. www.ispag.org/proceedings/?action=download&item=4970.
Sharma, V. 2019. Estimating Soil Moisture by Feel and Appearance Method. University of Minnesota Extension. https://extension.umn.edu/irrigation/estimating-soil-moisture-feel-and-appearance-method.
Virginia Cooperative Extension materials are available for public use, reprint, or citation without further permission, provided the use includes credit to the author and to Virginia Cooperative Extension, Virginia Tech, and Virginia State University.
Virginia Cooperative Extension is a partnership of Virginia Tech, Virginia State University, the U.S. Department of Agriculture (USDA), and local governments, and is an equal opportunity employer. For the full non-discrimination statement, please visit ext.vt.edu/accessibility.
Publication Date
July 21, 2021