Glue-Laminated Timber
ID
CNRE-151NP
What is Glulam?
Glue-laminated timber or glulam, is an engineered wood product consisting of several parallel layers of small pieces of lumber stacked and glued together under pressure to make a large timber structure (APA, 2019). Glulam is commonly used for structural components like columns, beams, and arches of mid to high-rise buildings. Glulam provides strength, stability, and various length options to facilitate design flexibility. Glulam adds beauty to the exposed structure section, like rafters and ridge beams. However, most of the beams are used as floor beams and headers and are invisible. Stock beams are the common types of glulam readily available in North America. Stock beams are used as floor beams, door or window headers, ridge and rafter beams, and columns.
Manufacturing of glue-laminated timber
The overall procedure of glulam manufacturing is shown in Figure 1. Logs are harvested and sawn to produce structural lumber. All sawn lumber is dried in a control system to the required moisture content of 16% and less, machine-graded, and sorted for lumber grade. All available softwood species and some hardwood species, like yellow poplar (Liriodendron tulipifera) are used to manufacture glulam in the US. Lumber is finger-jointed to get an ideal length of glulam and sent to surfacing before applying glue to form desired layups. Lumber is glued under pressure to form a solid wood product. After complete pressing, glulam is surfaced, packed, and sent to market. The major glulam manufactures form the US are listed in Table 1.
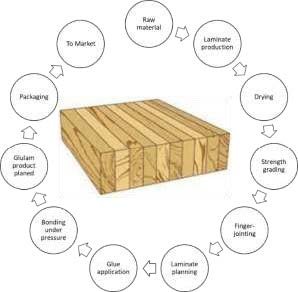
Manufacturers | City | State |
---|---|---|
Timber Technologies | Colfax | WI |
Structural Wood Systems | Greenville | AL |
Unalam | Unadilla | NY |
Arizona Structural Laminators | Eagar | AZ |
Boozer Laminated Beam Company | Anniston | AL |
Laminated Erectors | Trafalgar | IN |
Northway Industry Inc | Middleburg | PA |
Green Valley Beam & Truss Co. | Denton | TX |
Unadilla Laminated Products | Sidney | NY |
JR Lumber Company | Conneaut | OH |
84 Lumber | Dover | DE |
Mississippi Laminators | Shubuta | MS |
Dafor Heavy Timber Fabricators | Greenville | AL |
Calvert Company | Vancouver | WA |
Metkote Laminated Products Inc | Taylor | PA |
US Glu-Lam | Calumet | IL |
Kilby Truss Inc | Gray | TN |
Environmental impacts of glulam
Glulam is manufactured from locally available timber, so it is an environmentally sustainable construction material that helps in forest management. It promotes the wood industry at the local level. Thus, glulam adds minimum impact to the environment. The environmental impact of glulam is significantly less than steel and concrete. See Figure 2. Wood accumulates CO2 during its growth and sequestrates it in a structure for years. On the other hand, the production of steel and concrete only emits CO2 and negatively helps in the sequestration process.
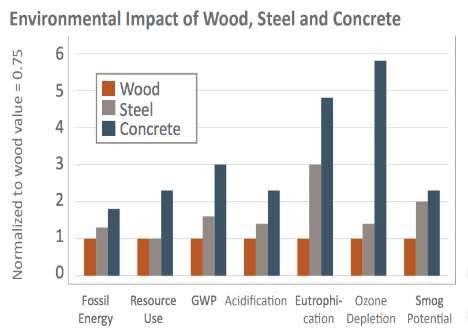
Advantages of Glulam
One of the design advantages of the glulam is the ease of bending into the desired curve shape and into long lengths. Glulam is manufactured by pressing small-length and specific width lumber through finger jointing. It can be set up to bend on the desired curve of any length and dimension for structural use. The ability to produce glulam of the required shape and size provides design flexibility and architectural and aesthetic beauty. The fire resistance of glulam timber is similar to normal wood as glulam acts as a thick wood member. See Figure 4. When the surface is ignited, the fire begins to penetrate the wood quickly. However, as the fire continues and a layer of char forms, the burn rate gradually decreases because the char acts as insulation, and also produces off-gassing that displaces the oxygen.
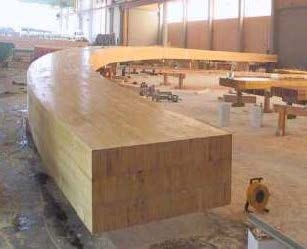
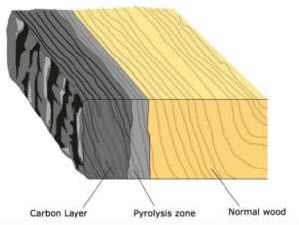
Availability of the product and variation in the dimension and shape is another advantage of glulam. Glulam is commercially available from 45 mm x 45 mm cross-section up to 250 mm x 1800 mm over 30 m lengths. The common glulam dimension based on its component is presented in Table 2. Additionally, based on lumber grade used to manufacture glulam, it is classified by stress class, as shown in Table 3. Working flexibility is another advantage of glulam. Due to its manufacturing advantage it can be used as beam and columns at any angle based on design specifications. See Figure 5. Also, glulam can be manufactured using different wood types (APA, 2008) that add additional texture, color, and character.
Glulam components | Spans (m) | Width (mm) | Height (mm) |
---|---|---|---|
Parallel beams | 6-32.5 | 100-260 | Max 2000 |
Double glued beams | 6-32.5 | 280-480 | Max 2000 |
Pre-cambered beams | 6-32.5 | 100-260 | 1000- 1840 |
Pent roof beams | 6-32.5 | 100-260 | Max 2000 |
Sloped beams with a straight bottom chord | 6-32.5 | 100-260 | Max 2000 |
Sloped beams with an arched bottom chord | 6-32.5 | 100-260 | Max 4500 |
Curved beams | 6-32.5 | 100-260 | Max 4500 |
Fish beam | 6-32.5 | 100-260 | Max 2000 |
Trusses | 15-50 | 100-260 | 1000- 1849 |
Free shapes | 6-32.5 | 100-260 | - |
Stress Class | Fbx+ (Kpa) | Fbx- (Kpa) | Fc⊥x (Kpa) | Fvx (Kpa) | Ex X106 (Kpa) |
---|---|---|---|---|---|
1 6F- 1 .3E | 1103 1 | 6377 | 2171 | 1344 | 8 |
20F- 1 .5E | 1378 9 | 7584 | 2930 | 1447 | 10 |
24F- 1 .7E | 1654 7 | 9997 | 3447 | 1447 | 11 |
24F- 1 .8E | 1654 7 | 9997 | 4481 | 1827 | 12 |
26B 1 .8E | 1792 6 | 13444 | 4481 | 1827 | 13 |
28F- 1 .8E | 1930 5 | 15857 | 5102 | 2068 | 14 |
30F-2.l E SP | 2068 4 | 16547 | 5102 | 2068 | 14 |
30F-2.l E LVL | 2068 4 | 20684 | 3516 | 2068 | 14 |
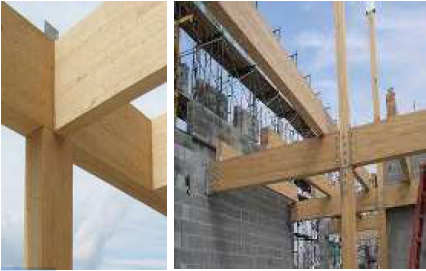
Glulam has 2-3 times higher durability than steel and concrete (James, 2020); on increasing pressure and tension, the wood gets adjusted to changing force due to its flexibility and withstands stress without damage. See Figure 6.
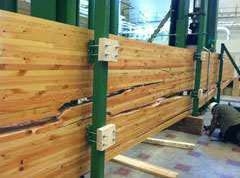
Glulam boards have better mechanical strength than other wood products and higher resistance to rot and fire.
Disadvantages of Glulam
There are some disadvantages of glulam, among them:
- Due to associated production costs, the Glulam price can be higher than other timber products.
- Availability of the product is another limitation as there are limited producers manufacturing glulam in the US.
- Glulam has lower moisture resistance than steel and concrete, thus it is designed with larger dimension components to reduce the moisture impact. Using larger dimension products adds more cost and material.
- Another limitation is the difficulty of repairing if required.
Acknowledgment
The Department of Sustainable Biomaterials at Virginia Tech would like to thank the Softwood Export Council (SEC) for providing the funding for the production of this fact sheet.
References
Aicher, S., & Stapf, G. (2014). Block Glued Glulam- Bridges, Beams and Arches.
https://doi.org/10.13140/2.1.3777.4720
Anthony Forest Products Co. (2021). Power Column.
https://www.anthonyforest.com/ewp/power-column.shtml
APA. (2008). Glulam Design Specification. www.CORRIM.org.
APA. (2019). Glulam Selection and Specification. www.apawood.org
APAEWS. (2004). Glulam Design Properties and Layup Combinations.
Architizer Journal. (2019). An Architect’s Guide to Glulam.
https://architizer.com/blog/productguides/product-guide/glulam/
CE Center. (2020). Connection Options for Wood- Frame and Heavy Timber Buildings.
https://continuingeducation.bnpmedia.com
CrossLam CLT. (2021). CLT Technical Design Guide Introduction.
James. (2020, August 24). Glue-laminated Timber Advantages and Disadvantages. Timber Blogger. https://www.timberblogger.com/gluelaminated-timber-advantages-anddisadvantages/
Naturally Wood. (2021). What is Glue-laminated timber (glulam)?
https://www.naturallywood.com/products/glulam/
SCS. (2021). GLULAM - Glued Laminated Timber».
http://www.cltcrosslaminatedtimber.com.au/products/glulam-glued-laminated-timber
Setra Group. (2021). Glulam Fire Safety. https://www.setragroup.com/en/glulam/
Spartz, J. t. (2013, January 28). Strength Testing of Glulam Beams Lab Notes.
https://www.fpl.fs.fed.us/labnotes/?p=72
Swedish Wood. (2021). Glulam and the environment.
https://www.swedishwood.com/buildingwith-wood/about-glulam/glulam-and-theenvironment/
Virginia Cooperative Extension materials are available for public use, reprint, or citation without further permission, provided the use includes credit to the author and to Virginia Cooperative Extension, Virginia Tech, and Virginia State University.
Virginia Cooperative Extension is a partnership of Virginia Tech, Virginia State University, the U.S. Department of Agriculture, and local governments. Its programs and employment are open to all, regardless of age, color, disability, sex (including pregnancy), gender, gender identity, gender expression, genetic information, ethnicity or national origin, political affiliation, race, religion, sexual orientation, or military status, or any other basis protected by law.
Publication Date
May 9, 2022