Structural Composite Lumber (SCL)
ID
CNRE-152NP
What is SCL?
Structural composite lumber (SCL) is an engineered wood product manufactured by layering strands, veneers, or flakes with adhesive into material blocks known as billets. The term SCL was used to capture the variety of unique structural products that include parallel strand lumber (PSL), laminated strand lumber (LSL), laminated veneer lumber (LVL), and oriented strand lumber (OSL). For all SCL billets, the grain of each layer ran in the same direction. SCL has been successfully used for various construction purposes, including headers, truss chords, rafters, beams, joists, columns, I-joist flanges, and wall studs.
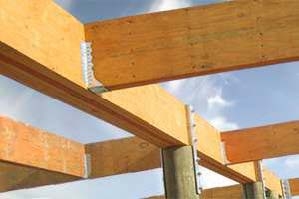
SCL is manufactured to some standard size, then resawn into specified sizes based on the product end- use. Some SCL products are available in several thicknesses, while others are only produced in standard 45 mm thickness. Typical depths of SCL members range from 241 to 606 mm. Single SCL members may be nailed or bolted together to form built-up beams. Generally, SCL is available in lengths of up to 20 m. Some of the major SCL producers from the US are listed in Table 1.
Manufactures | City | State |
---|---|---|
Boise Cascade Company | Boise | Idaho |
Roseburg Forest Products Company | Roseburg | Oregon |
Murphy Company | Eugene | Oregon |
Pacific Woodtech Corporation | Burlington | Washington |
Sound Wood Products Inc | Chehalis | Washington |
Roseburg South Engineered Wood | Roseburg | Oregon |
Freres Lumber Co Inc. | Lyons | Oregon |
Design Specification of SCL
SCL is a proprietary product, so each manufacturer's design value is specific. Using SCL in the structural application requires information on the design properties of each product type specific to the company. As an example, the design values of different SCL types from Weyerhaeuser are included in Table 2.
Laminated veneer lumber (LVL)
LVL is manufactured from thin veneer layers to form larger beams and columns. These layers are glued together under high pressure and heat to make solid panels. In LVL, the grain of each veneer layer runs in the same direction so that it can be loaded on its short edge as a beam or as a plank in a wide face. Generally, LVL is made from rotary-peeled veneers. A diverse range of species can be used to produce LVL, such as pine, larch, Douglas-fir, and spruce. Because of the material choice and production procedure of LVL, they are stronger, straighter, and more uniform than solid timber. LVL has primarily been used in structural framing for residential and commercial construction. Common applications of LVL in construction include hip and valley rafters, flange material for prefabricated wood I-joists headers and beams, and scaffold planking. LVL has been used in roadway signposts and as truck bed decking. First used during World War II to make airplane propellers, laminated veneer lumber (LVL) has been available as a construction product since the mid-1970s. LVL is the most widely used structural composite lumber (SCL) product because of its strong dimensional attributes and rigidity.
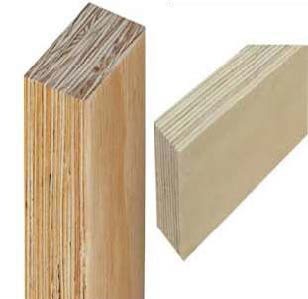
The LVL panels are cut into a range of widths depending on the product's end-use. The most common thickness of LVL is 45 mm but LVL thicknesses vary from 19 mm to 178 mm. Manufacturers commonly produce the LVL with standardized depths of 241 mm, 302 mm, 356 mm, 406 mm, 476 mm, and 606 mm. Wider beams are constructed by attaching multiple LVL plies. LVL is also available in lengths up to 24.4 m, while more common lengths are 14.6 m, 17 m, 18.3 m, and 20.1 m.
Laminated strand lumber (LSL)
LSL is another engineered wood product made from flaked wood strands with a length-to-thickness ratio of approximately 150. The strands are oriented and formed into a large mat or billet before applying glue with heat and pressure to convert into solid wood. The strands in LSL are set up parallel to the member's longitudinal axis, which is different from OSB. LSL also does not have a common standard of production and common design values.
LSL is predominantly used in structural framing for commercial, residential, and industrial construction. It is appropriate for millwork, tall wall studs, headers and beams, sill plates, rim boards, and window framing. LSL has good fastener-holding strength and provides design flexibility for exposed parts.
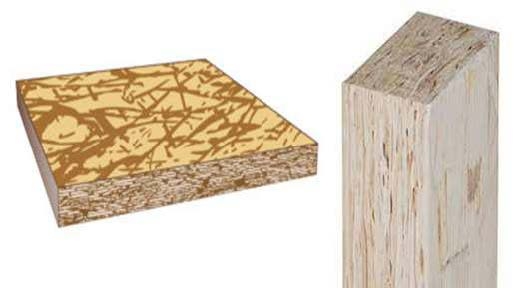
Oriented strand lumber (OSL)
OSL is made from flaked wood strands with a length-to-thickness ratio of approximately 75. The wood strands used in OSL are shorter than those in LSL. The strands are oriented and formed into a large billet to get the solid wood product after applying glue under heat and pressing. OSL looks like an oriented strand board (OSB) in physical appearance. They are both fabricated from similar wood species and contain flaked wood strands. However, unlike OSB, the strands in OSL are arranged parallel to the member's longitudinal axis.
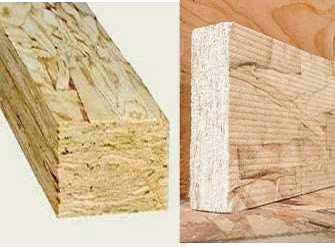
Parallel strand lumber (PSL)
PSL is a solid engineered wood product. It is made from flaked wood strands arranged parallel to the member's longitudinal axis and has a length-to-thickness ratio of approximately 300. Combined with an exterior waterproof phenol-formaldehyde adhesive, the strands are oriented and formed into a large billet, then pressed together and cured using microwave radiation. Natural defects such as knots, grain slope, and splits have been distributed all over the material or removed entirely during manufacturing.
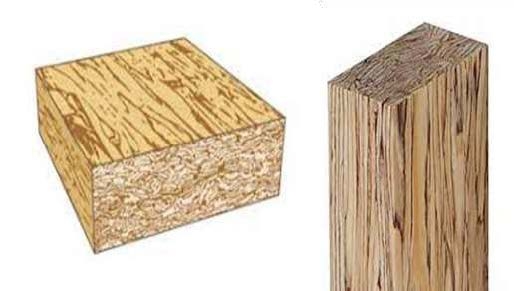
PSL also does not have a common standard of production and common design values, so it is specific to manufacturers. PSL beams are available in 68 mm, 89 mm, 133 mm, and 178 mm thickness and a maximum depth of 457 mm. PSL columns are available in 89 mm, 133 mm, and 178 mm square or rectangular dimensions. The smaller thicknesses can be used individually as single plies or combined for multi-ply applications. PSL is usually limited to 20 m in length due to transportation constraints. PSL is the only SCL type that can be pressure treated and used outside in an exposed environment.
Why use SCL?
- The major advantage of SCL in the US is that it is available through lumber distribution systems, so availability is not an issue as it might be with glulam.
- SCL helps to meet the increasing demand for structural lumber products with highly reliable strength and stiffness properties. Because of material choice and production procedure, SCL products can take greater loads than the sawn timber equivalent.
- SCL is much less prone to warping, splitting, or shrinking when compared to sawn timber, so it offers structural integrity and stability.
- SCL offers more diversity in sizes and dimensions and provides working flexibility.
- SCL is a highly sustainable product, as they sequester significant amounts of carbon and increase the energy efficiency of the building.
- SCL utilizes a higher percentage of scraps from timber production. Reusing these valuable resources reduces the amount of timber harvesting required to maintain adequate production levels, which preserves more forest area.
- With its ability to be manufactured using small, fast-growing, and underutilized trees, SCL products efficiently use forest resources and help in forest management.
- SCL also offers efficiency in the installation process's working time and labor costs. Some SCL types offer the lowest density products at maximum strength, assisting in lowering foundation work and cost.
Limitations of using SCL
- The cost of the SCL is a major concern to many builders. As SCL adds more labor time and processing work during its production, they are comparatively costlier than structural grade lumber though the cost per strength of SCL higher than structural lumber.
- SCL studs are usually denser and heavier than structural grade lumber, so they're more difficult to nail.
- Wood does not like moisture and water exposure, and especially SCL can't stand exposure to humidity. After exposure to moisture, SCL easily discolors, warps, expands, and rots faster than dimensional lumber.
- In most cases, the manufacturing process involves the usage of urea-formaldehyde resin, and it makes the boards toxic.
Acknowledgment
The Department of Sustainable Biomaterials at Virginia Tech would like to thank the Softwood Export Council (SEC) for providing the funding for the production of this fact sheet.
References
APA. (2021). Structural Composite Lumber (SCL) - APA – The Engineered Wood Association. https://www.apawood.org/structural-composite-lumber
Chirag Enterprises. (2021). Laminated Veneer Lumber LVL Board. https://www.indiamart.com/proddetail/laminated-veneer-lumber-19724343155.html
CWC. (2021a). Laminate Veneer Lumber - The Canadian Wood Council - CWC. https://cwc.ca/en/how-to-build-with-wood/wood-products/structural-composite/laminate-veneer-lumber/
CWC. (2021b). Laminated Strand Lumber - The Canadian Wood Council - CWC. https://cwc.ca/en/how-to-build-with-wood/wood-products/structural-composite/laminated-strand-lumber/
CWC. (2021c). Oriented Strand Lumber - The Canadian Wood Council - CWC. https://cwc.ca/en/how-to-build-with-wood/wood-products/structural-composite/oriented-strand-lumber
CWC. (2021d). Parallel Strand Lumber - The Canadian Wood Council - CWC. https://cwc.ca/en/how-to-build-with-wood/wood-products/structural-composite/parallel-strand-lumber/
Intense Research. (2021). Global and China Oriented Strand Lumber Market 2016 Size, Key Trends, Demand, Growth, Size, Review, Share, Analysis to 2021 2016-05-02.
https://www.pr-inside.com/global-andchina-oriented-strand-lumber-market-201-r4424279.htm
Naturally Wood. (2021a). What is Laminated Strand Lumber (LSL)? - naturally: wood. https://www.naturallywood.com/products/laminated-strand-lumber/
Naturally Wood. (2021b). What is Parallel Strand Lumber (PSL)?
https://www.naturallywood.com/products/parallel-strand-lumber/
Weyerhaeuser. (2021). Design information for TimberStrand LSL, Microllam LVL and Parallam PSL. https://www.weyerhaeuser.com/woodproducts/document-library/
SCL Product | TimberStrand® LSL | ||
---|---|---|---|
SCL Grade | 1.3 E | 1.55E | |
Orientation | Beam/Column | Plan | Beam |
G (Shear Modulus of Elasticity) -Kpa | 560,199 | 560,199 | 667,929 |
E (Modulus of Elasticity x 106) -Kpa | 8 | 8 | 10 |
Emin (Adjusted Modulus of Elasticity) -Kpa | 4,555,710 | 4,555,710 | 5,431,792 |
Fb (Flexural Stress) -Kpa | 11,721 | 13,100 | 16,030 |
Ft (Tension Stress) -Kpa | 8,963 | 8,963 | 8,894 |
Fc⊥ (Compression Perpendicular to Grain) -Kpa | 4,895 | 4,619 | 6,205 |
Fcll (Compression Parallel to Grain) -Kpa | 12,651 | 12,651 | 14,961 |
Fv (Horizontal Shear Parallel to Grain) -Kpa | 2,930 | 1,034 | 2,137 |
SG (Specific Gravity) | 0.5 | 0.5 | 0.5 |
SCL Product | Microllam® LVL | Parallam® PSL | |
SCL Grade | 2.0E | 1.8E | 2.2E |
Orientation | Beam | Column | Beam |
G (Shear Modulus of Elasticity) -Kpa | 861,844 | 775,660 | 948,029 |
E (Modulus of Elasticity x 106) -Kpa | 13 | 12 | 15 |
Emin (Adjusted Modulus of Elasticity) -Kpa | 7,008,761 | 6,307,875 | 7,709,648 |
Fb (Flexural Stress) -Kpa | 17,926 | 16,547 | 19,994 |
Ft (Tension Stress) -Kpa | 1,3065 | 13,755 | 15,857 |
Fc⊥ (Compression Perpendicular to Grain) -Kpa | 5,171 | 3,757 | 4,309 |
Fcll (Compression Parallel to Grain) -Kpa | 1,7305 | 17,236 | 19,994 |
Fv (Horizontal Shear Parallel to Grain) -Kpa | 1,965 | 1,310 | 1,999 |
SG (Specific Gravity) | 0.5 | 0.5 | 0.5 |
Virginia Cooperative Extension materials are available for public use, reprint, or citation without further permission, provided the use includes credit to the author and to Virginia Cooperative Extension, Virginia Tech, and Virginia State University.
Virginia Cooperative Extension is a partnership of Virginia Tech, Virginia State University, the U.S. Department of Agriculture, and local governments. Its programs and employment are open to all, regardless of age, color, disability, sex (including pregnancy), gender, gender identity, gender expression, genetic information, ethnicity or national origin, political affiliation, race, religion, sexual orientation, or military status, or any other basis protected by law.
Publication Date
May 9, 2022